Compressors, as one of the essential pieces of equipment in industrial production, directly affect operational costs, maintenance expenses, and environmental sustainability. This article provides a comprehensive discussion on compressor energy efficiency levels, including their definition, classification, evaluation standards, influencing factors, and measures for improving energy efficiency. It aims to guide businesses in selecting and utilizing compressors efficiently.
The energy efficiency of compressors is assessed through Specific Energy Consumption (SEC) and Energy Efficiency Ratio (EER), which reflect the relationship between the electrical energy consumed during compressed air production and the output. The classification of energy efficiency levels varies according to regional standards, with European standards ranging from A+++ to D, the U.S. using Energy Star certification, and China setting five levels (A to E).
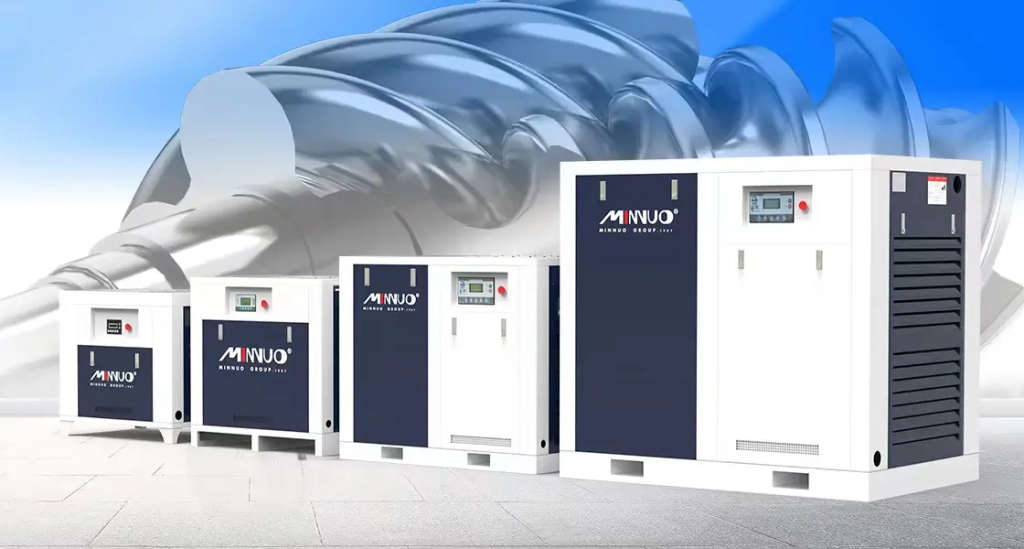
1. Definition of Compressor Energy Efficiency Levels
Compressor energy efficiency levels are evaluated based on the relationship between the energy consumed during compressed air production and the output of compressed air. Simply put, a more energy-efficient compressor uses less energy to meet the same production demands. Energy efficiency is typically represented by Specific Energy Consumption (SEC) or Energy Efficiency Ratio (EER). These indicators help businesses understand the energy consumption of compressors and make more economical choices.
Energy efficiency levels are crucial for companies, as they directly impact production costs, equipment maintenance expenses, energy costs, and environmental pressure. In industrial production, compressors often represent a significant portion of energy consumption. Selecting the right compressor not only enhances production efficiency but also reduces energy expenses.
2. Classification of Compressor Energy Efficiency Levels
The classification of compressor energy efficiency levels is typically based on standards from different countries and regions. Here are some common classification methods:
2.1 European Energy Efficiency Levels (EU)
In Europe, compressor energy efficiency standards are set by the European Union and marked through the “Energy Label.” According to EU standards, compressors’ energy efficiency levels range from A+++ (most energy-efficient) to D (least efficient). The efficiency level is determined based on the energy usage efficiency during the compression process and the power consumption while operating. A+++ compressors provide high compressed air output with low power consumption, making them the most energy-efficient compressors available on the market.
2.2 U.S. Energy Efficiency Levels (US)
In the U.S., compressor energy efficiency standards are set by the Department of Energy (DOE) and Energy Star, among other organizations. The Energy Star label certifies compressors that meet high energy efficiency standards. U.S. efficiency standards primarily evaluate compressors based on Specific Energy Consumption (SEC) and Energy Efficiency Ratio (EER).
2.3 Chinese Energy Efficiency Levels (CN)
In China, compressor energy efficiency standards are set by the government, specifically in the GB 19153 standard, “Energy Efficiency Limits and Energy Efficiency Levels for Compressed Air Equipment.” According to this standard, compressors are classified into five levels, ranging from A (most energy-efficient) to E (least efficient). China’s standards have stringent energy efficiency requirements, especially for low-efficiency compressors, to encourage energy-saving and emission-reduction efforts.
3. How to Evaluate Compressor Energy Efficiency
Compressor energy efficiency is primarily evaluated through the following indicators:
3.1 Energy Efficiency Ratio (EER)
Energy Efficiency Ratio (EER) is a crucial evaluation metric for compressor energy efficiency, indicating the amount of electrical energy consumed to produce each unit of compressed air. The higher the EER, the lower the power consumption for each unit of compressed air output, meaning higher energy efficiency. EER is often used to measure a compressor’s power consumption during operation, making it an important standard for evaluating energy efficiency. For example, the EER value of MINNUO’s variable frequency compressor is 5.2, a 30% improvement over standard models, meaning more power savings for the same air output.
3.2 Specific Energy Consumption (SEC)
Specific Energy Consumption (SEC) refers to the amount of electrical energy consumed to produce a unit of compressed air. The lower the SEC, the higher the energy efficiency and the lower the energy consumption of the compressor under the same operating conditions. SEC is another key metric for evaluating compressor energy efficiency, often used to compare the energy consumption performance of different compressors in actual work.
3.3 Continuous Operating Efficiency
Continuous operating efficiency refers to the compressor’s ability to maintain efficient operation over extended periods. A high-efficiency compressor should be able to maintain stable energy efficiency under varying loads and working conditions, without significant fluctuations due to environmental changes (e.g., temperature, humidity). MINNUO compressors, equipped with intelligent control systems, maintain energy efficiency fluctuations below 3% in environments ranging from -10°C to 50°C and with load fluctuations from 30% to 100%, ensuring long-term stable operation.
4. Importance of Compressor Energy Efficiency Levels
Compressor energy efficiency levels have significant implications for businesses and the environment, as outlined below:
4.1 Reducing Energy Costs
The energy efficiency of compressors directly determines the energy consumption of the equipment, which affects operational costs. Compressor power consumption is often a major expenditure in industrial production. Choosing energy-efficient compressors can significantly reduce electricity consumption, thereby lowering energy costs for businesses. Over the long term, this not only helps improve competitiveness but also enhances profit margins.
4.2 Reducing Environmental Impact
With global warming and environmental issues becoming increasingly critical, companies are under more pressure to address their environmental impact. Energy-efficient compressors can reduce energy consumption and greenhouse gas emissions, such as carbon dioxide, helping businesses fulfill their social responsibility and reduce their carbon footprint. Therefore, selecting energy-efficient compressors helps companies contribute to environmental sustainability.
4.3 Improving Equipment Stability and Service Life
Energy-efficient compressors often utilize advanced technologies and designs, enabling them to maintain stable performance over long operating periods. This not only improves operational efficiency but also reduces the failure rate of equipment, lowering maintenance and replacement costs. Additionally, energy-efficient compressors experience less overheating and wear, leading to a longer service life.
4.4 Enhancing Brand Image
With the growing emphasis on energy-saving and emission-reduction practices, more businesses and consumers are paying attention to the energy efficiency of products. Selecting energy-efficient compressors can help companies reduce operating costs and improve their market image, showcasing their commitment to environmental protection and corporate social responsibility.
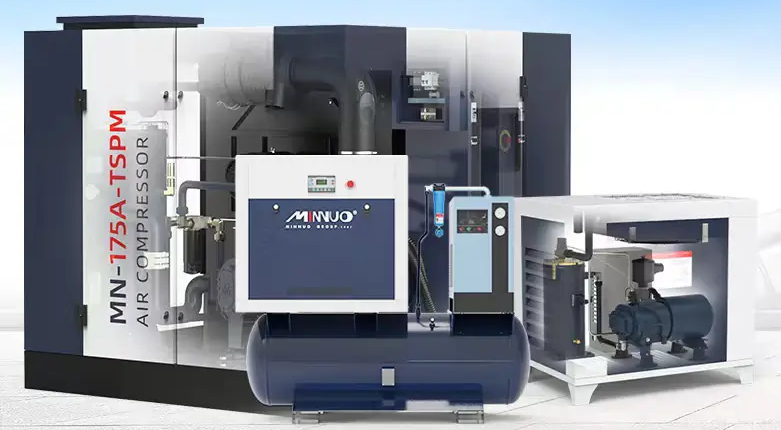
5. How to Choose an Energy-Efficient Compressor
When selecting an energy-efficient compressor, businesses need to consider the following factors:
5.1 Type of Compressor
Compressors are classified according to their working principles and suitable applications. Common types include piston compressors, screw compressors, and centrifugal compressors. The energy efficiency of these compressors varies under different operating conditions. Piston compressors are suitable for low-flow demands, screw compressors are suitable for medium-flow needs, and centrifugal compressors are best for large-scale industrial production. Choosing the right type of compressor is key to improving energy efficiency.
5.2 Consider Load Fluctuations
In real production processes, air demand may fluctuate. To enhance energy efficiency, businesses should choose compressors that can adapt to load changes. Variable speed drive (VSD) compressors can automatically adjust the motor speed based on actual air demand, preventing the compressor from running at high energy consumption levels during low-load conditions, significantly improving energy efficiency.
5.3 Check Energy Efficiency Certification and Labels
When selecting compressors, businesses should check for energy efficiency labels or certifications. Compressors that meet international energy efficiency standards typically offer higher energy efficiency, helping to reduce energy consumption and lower production costs.
5.4 Consider Maintenance and Operating Environment
Compressor maintenance is another key factor affecting its energy efficiency. Regular maintenance ensures that compressors operate efficiently and prevents energy efficiency from decreasing due to equipment failure or dust accumulation. Additionally, the operating environment can affect compressor performance. Maintaining optimal temperature, humidity, and air quality helps the compressor operate more efficiently.
6. MINNUO’s Six Efficiency Enhancement Strategies
Improving compressor energy efficiency is not only about selecting efficient equipment, but also optimizing the system’s operation through various measures:
6.1 Use of Variable Speed Drives (VSD)
Variable speed drive technology automatically adjusts the motor’s speed based on demand, avoiding inefficient operation at low loads and reducing energy waste.
6.2 Install Air Storage Tanks
Installing air storage tanks can effectively regulate system pressure, reduce compressor starts and stops, and avoid operating at low loads, thereby reducing energy consumption.
6.3 Optimize Piping Design
Optimizing the layout of compressor system piping reduces pressure losses in the air flow, which helps enhance the system’s overall energy efficiency.
6.4 Regular Maintenance
Regular inspections and maintenance of compressors, including cleaning air filters, checking lubrication oils, and inspecting cooling systems, ensure that compressors remain in optimal operating condition and prevent energy efficiency decline due to equipment failures.
7. Conclusion
When selecting compressors, businesses should focus on their energy efficiency levels, choose equipment that meets energy efficiency standards, and implement effective optimization measures to enhance the overall energy efficiency of the system.
MINNUO is committed to driving energy-saving technology upgrades with over 30 years of industry experience and a global R&D team. We provide customers with a full range of solutions, from equipment selection and system design to operational services. Contact MINNUO today to get your exclusive energy-saving plan and start a new chapter in cost reduction and efficiency improvement!