In industrial production, compressed air not only powers equipment and facilitates processes but also directly impacts product quality and operational safety. Oil-injected and oil-free compressors, as two key types of equipment, differ significantly in lubrication methods, air quality, certification standards, and applicable scenarios. This article provides a comprehensive analysis of both.
Oil-injected compressors improve operational efficiency by injecting lubricating oil, but traces of oil remain in the compressed air. In contrast, oil-free compressors utilize special designs to eliminate oil contamination, achieving ISO Class 0 certification, making them suitable for industries with strict purity requirements. While oil-injected models have a lower initial cost, they rely on filtration systems for maintenance, potentially increasing long-term risks. Oil-free compressors, despite higher upfront investment, reduce maintenance needs and contamination risks.
1. Lubrication Methods and Compressed Air Quality
1.1 Fundamental Differences in Lubrication Mechanisms
Oil-Injected Compressors
Oil-injected compressors introduce lubricating oil (such as screw compressor oil) into the compression chamber during operation to provide lubrication, cooling, and sealing. The oil film reduces mechanical wear and enhances efficiency, but it also results in inevitable oil contamination in the compressed air. Although multi-stage filtration systems like oil separators and activated carbon filters help remove oil droplets, they cannot completely eliminate oil vapors and trace contamination.
Oil-Free Compressors
Oil-free compressors are designed to eliminate lubricating oil usage within the compression chamber. They achieve friction control and cooling through methods like water cooling, special coatings (e.g., Teflon), or stainless steel components. For example, oil-free screw compressors use non-contact twin-screw designs with synchronized gears controlling rotor clearance, while oil-free piston compressors employ Teflon-coated piston rings to prevent oil contamination. The purity of their compressed air can reach ISO Class 0, with an almost negligible total oil content, making them ideal for applications requiring the highest air quality.
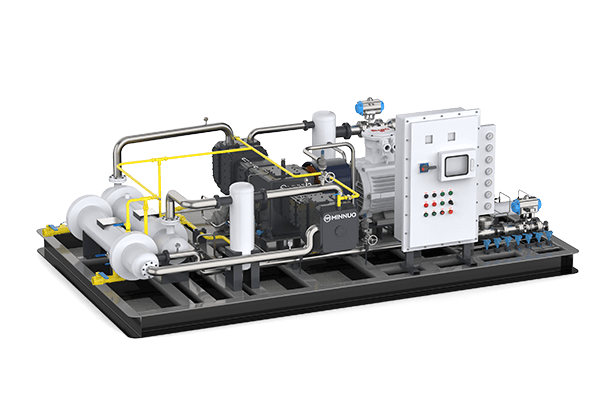
1.2 Air Quality Comparison
Oil-Injected Compressors
After high-efficiency filtration, the oil content in compressed air is typically controlled at approximately 0.01 mg/m³ (ISO Class 1). However, filtration systems primarily test airflow at the center (B2 testing), which may not fully capture oil residue adhering to pipe walls or oil vapors, leaving a risk of contamination.
Oil-Free Compressors
Oil-free compressors undergo full-flow (B1) testing, ensuring compressed air is free from liquid oil, aerosols, and oil vapors. They achieve the stringent ISO Class 0 standard, providing absolute air purity for sensitive applications such as pharmaceuticals and food processing.
2. Certification Standards and Technical Controversies
2.1 ISO 8573-1 Standard and Certification Categories
The International Organization for Standardization (ISO) has established the ISO 8573-1 standard, which classifies compressed air quality levels (ISO 0–ISO 5) based on oil, solid particle, and moisture content.
- Class 0 (True Oil-Free): Ensures compressed air contains no oil contamination in any form. Oil-free compressors pass full-flow B1 testing, which covers both the airflow center and pipe walls, guaranteeing air purity suitable for industries with the highest safety requirements.
- Class 1 and Below (Technically Oil-Free): Oil-injected compressors achieve “oil-free” performance through multi-stage filtration but only test oil droplets in the airflow center (B2 testing). This method carries a residual risk of oil and vapor contamination.
2.2 Technical Controversies and Common Misconceptions
Misconception 1: “Technically Oil-Free = True Oil-Free”
Some believe that oil-injected compressors combined with high-efficiency filtration can achieve oil-free performance. However, in high-temperature environments (e.g., at an ambient temperature of 30°C, with an outlet temperature reaching 40°C), oil vapor levels can surge up to 20 times higher. If filters fail or are improperly maintained, sudden contamination can occur, causing irreversible damage to sensitive applications.
Misconception 2: “Filters Provide Higher Air Quality Than Oil-Free Compressors”
Although activated carbon filters can reduce oil content to extremely low levels (e.g., 0.003 mg/m³), high maintenance costs, filter lifespan reductions due to temperature increases (up to 90% shorter at higher temperatures), and the lack of a failure warning mechanism make this approach riskier in long-term operation.
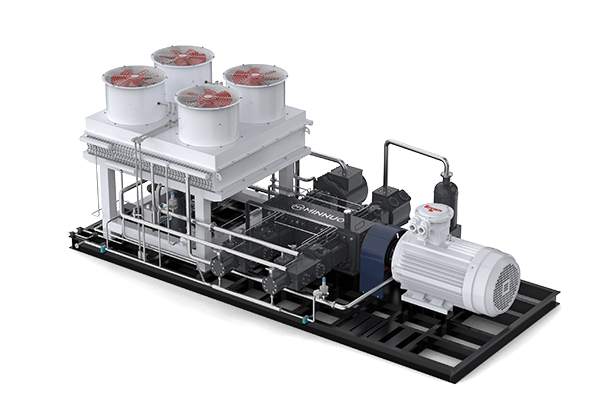
3. Equipment Characteristics and Application Scenarios
3.1 Performance and Cost Comparison
Parameter | Oil-Injected Compressor | Oil-Free Compressor |
Initial Cost | Lower | Higher (due to specialized materials and processes) |
Maintenance Cost | Requires regular filter and oil changes; depends on maintenance management | No oil-related maintenance; simpler overall maintenance |
Energy Consumption | Pressure drops from multi-stage filters may increase energy usage | High-efficiency designs (e.g., variable frequency drive) lead to lower energy consumption |
Noise Level | Lower due to oil film damping | Higher due to design; may require noise reduction measures |
3.2 Core Application Fields
Oil-Free Compressors:
- Medical and Pharmaceuticals: Ensures sterile, contamination-free medical air.
- Food and Beverage Processing: Prevents oil contamination, ensuring food safety.
- Electronics Manufacturing: Maintains ultra-clean environments, preventing particle contamination.
- Chemical and High-Purity Reactions: Ensures precision and product purity.
Oil-Injected Compressors:
- Mining, Metallurgy, and Heavy Industries: Tolerates trace oil contamination.
- General Machining and Manufacturing: Prioritizes cost-effectiveness while meeting basic production needs.
4. Oil-Free Compressor Technologies and Types
Oil-free compressors can be categorized based on their operating principles:
Oil-Free Screw Compressors
Utilize a non-contact twin-screw design, where synchronized gears control rotor clearance, eliminating the need for lubricating oil. Multi-stage compression and inter-stage cooling enhance pressure range and operational stability.
Oil-Free Piston Compressors
Replace lubricating oil with Teflon-coated piston rings, effectively controlling friction while isolating the crankcase from the compression chamber to prevent oil vapor infiltration.
Oil-Free Scroll Compressors
Compress air through the relative motion of spiral-shaped rotors and a fixed scroll body. Their compact structure and low noise levels make them suitable for small to mid-range applications.
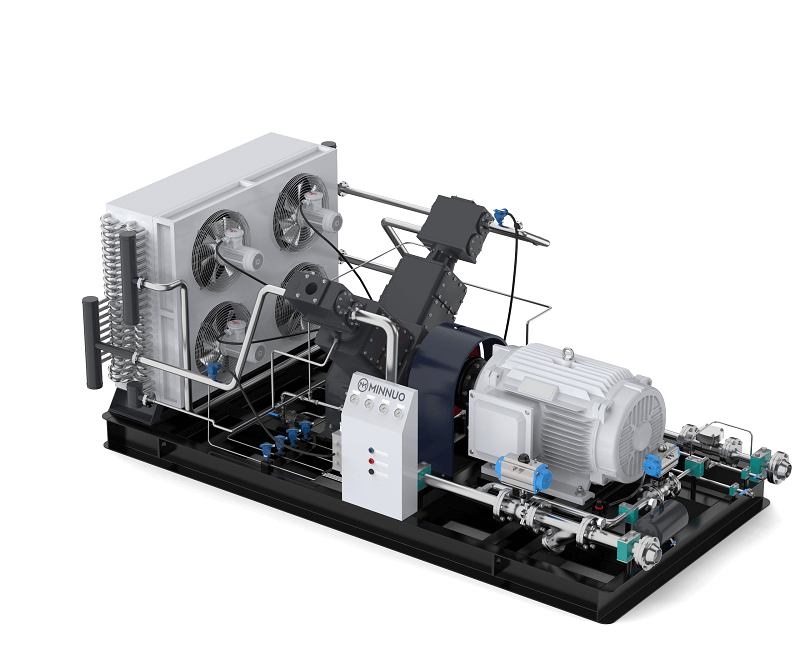
5. Selection Recommendations and Risk Mitigation
5.1 Matching Requirements to ISO Standards
- For sensitive industries (e.g., medical, food, electronics, pharmaceuticals), ISO Class 0-certified oil-free compressors are essential to guarantee air purity and prevent risks like product recalls, equipment damage, or environmental hazards.
- For applications permitting trace oil contamination (e.g., heavy industries, general manufacturing), oil-injected compressors with multi-stage filtration can meet production needs. However, strict maintenance schedules must be followed to ensure optimal performance.
5.2 Environmental and Long-Term Cost Considerations
- Temperature Impact: Oil-injected compressors produce significantly more oil vapor in high-temperature environments, whereas oil-free compressors remain unaffected.
- Total Cost of Ownership: While oil-free compressors require a higher initial investment, they eliminate filter replacements, oil management, and related maintenance costs. Conversely, oil-injected compressors require frequent maintenance, posing a risk of production failures due to filter malfunctions.
6. Conclusion
Choosing between oil-injected and oil-free compressors ultimately involves balancing risk and cost. For industries requiring the highest levels of compressed air purity, only ISO 8573-1 Class 0 oil-free compressors ensure absolute safety and reliability. In applications where minor oil contamination is acceptable and budget constraints exist, oil-injected compressors may be a more economical choice.
Regardless of the selection, businesses must conduct thorough evaluations based on process requirements, environmental conditions, and maintenance capabilities to avoid costly technical misunderstandings. Choosing the right technical team is crucial—MINNUO has over 30 years of compressor manufacturing experience, making MINNUO the professional choice.