In the realm of precision machining in modern manufacturing, laser cutting technology has become an indispensable processing method due to its significant advantages of high precision, efficiency, and flexibility. The close collaboration of core equipment such as nitrogen generators and nitrogen compressors provides strong support for the superior performance of laser cutting. A deep exploration of the application of nitrogen in laser cutting is of great significance for improving the processing quality and efficiency across various industries.
As an inert gas, nitrogen does not easily react with materials at high temperatures, effectively preventing oxidation reactions, reducing the formation of oxide layers during the cutting process, and ensuring better cutting surface quality. Additionally, nitrogen can provide higher cutting speeds and finer cutting results, especially in metal cutting where precision is critical. With the assistance of nitrogen, laser cutting can reduce the heat-affected zone, thereby improving processing efficiency and quality. Nitrogen generators and nitrogen compressors are key equipment in this process.
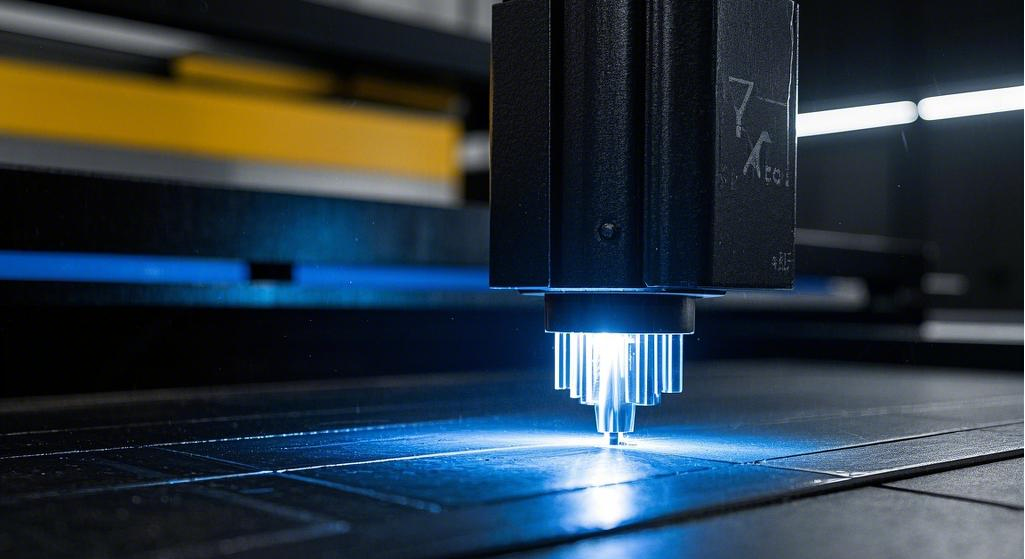
1. Fundamentals of Nitrogen Application in Laser Cutting
(1) Advantages of Nitrogen’s Properties
Nitrogen is an inert gas with highly stable chemical properties. The triple bond in its molecular structure has a bond energy of up to 941.69 kJ/mol, making it extremely difficult for nitrogen to react with other substances under normal conditions. This stability is particularly crucial in the high-temperature, high-energy environment of laser cutting. From a chemical thermodynamics perspective, under most laser cutting conditions, the Gibbs free energy change (ΔG) for nitrogen participating in reactions is positive. According to the criterion for spontaneous reactions:
ΔG = ΔH – TΔS
(where ΔH is enthalpy change, T is thermodynamic temperature, and ΔS is entropy change), it is clear that the reaction is unlikely to occur spontaneously, which fundamentally explains its stability.
Moreover, nitrogen’s non-flammability gives it inherent explosion-proof properties in laser cutting environments. According to the theory of explosive limits, the concentration range of a flammable gas mixed with air that can cause an explosion upon ignition is called the explosive limit. The presence of nitrogen dilutes the concentration of flammable gases, keeping it below the lower explosive limit, significantly reducing the risk of explosion. This makes nitrogen the preferred choice for many companies to ensure safe production and processing quality.
(2) Universality of Application
Nitrogen is widely used in the laser cutting of various metal materials such as carbon steel, stainless steel, and aluminum alloys, as well as some non-metal materials like acrylic and wood. From the machining of components in large-scale manufacturing enterprises to precision cutting in electronics manufacturing, nitrogen is ubiquitous. Its widespread application underscores its importance in the field of laser cutting. In metal cutting, nitrogen-assisted cutting processes help improve cutting quality and precision. In non-metal cutting, nitrogen protects the cutting area and prevents material carbonization. According to relevant industry research reports, over 80% of aerospace component manufacturers use nitrogen-assisted laser cutting to ensure the high precision and quality requirements of their parts.
2. Key Roles of Nitrogen in Laser Cutting
(1) Improving Cutting Quality
During laser cutting, nitrogen as an auxiliary gas effectively blows away molten slag and debris, preventing the slag from reattaching to the cutting surface, thereby significantly improving the flatness and smoothness of the cut. For precision components with extremely high surface quality requirements, such as engine blades in the aerospace industry or precision medical device parts, nitrogen-assisted cutting ensures that the cutting surface meets the required roughness specifications. According to surface roughness standards (such as Ra, Rz parameters), nitrogen-assisted cutting can reduce the Ra value of the cutting surface by 30%-50%, effectively reducing the need for subsequent grinding and polishing processes and improving production efficiency.
Nitrogen also inhibits oxidation reactions during cutting. When cutting carbon steel, using oxygen as an auxiliary gas can cause an oxide layer to form on the cutting surface, affecting the corrosion resistance and surface quality of the cut piece. Nitrogen’s inertness effectively prevents oxidation, enabling oxidation-free cutting, resulting in a smooth, oxide-free surface that retains the material’s original mechanical properties. From a chemical kinetics perspective, the oxidation reaction rate between oxygen and metal at high temperatures is rapid. The presence of nitrogen significantly reduces the oxygen concentration, and according to the reaction rate equation :
v = kCAnCBm
(where v is the reaction rate, k is the rate constant, CA and CB are reactant concentrations, and n and m are reaction orders), the reduction in oxygen concentration CA leads to a significant decrease in the oxidation reaction rate v, thereby effectively inhibiting oxidation.
(2) Enhancing Cutting Efficiency
Appropriate nitrogen pressure and flow rate can quickly expel molten slag from the cutting area, reducing the absorption and scattering of laser beam energy by the slag, allowing the laser beam to act more effectively on the cutting material and increasing cutting speed. For example, when cutting thicker plates, nitrogen’s excellent slag removal effect prevents slag accumulation in the cutting seam, enabling faster cutting speeds and higher production efficiency. From a heat transfer perspective, the heat exchange between nitrogen and the cutting area follows Newton’s law of cooling:
(where q is heat flux, h is the convective heat transfer coefficient, A is the heat transfer area, Tw is the wall temperature, and Tf is the fluid temperature).
High-velocity nitrogen has a high convective heat transfer coefficient h, rapidly removing heat q from the cutting area and lowering the material temperature Tw, preventing material deformation due to overheating. This ensures cutting precision while also improving cutting efficiency, as there is no need to frequently adjust cutting parameters or pause cutting due to thermal deformation issues.
(3) Expanding the Range of Cuttable Materials
For certain special materials, such as stainless steel and aluminum alloys, nitrogen-assisted cutting offers unique advantages. When cutting stainless steel, nitrogen prevents the formation of a nitride layer on the cutting surface, avoiding any impact on the material’s corrosion resistance. When cutting aluminum alloys, nitrogen reduces burrs and slag during the cutting process, improving cutting quality and enabling the processing of materials that are otherwise difficult to cut. This expands the application range of laser cutting technology, meeting the needs of various industries for processing special materials.
This involves the interaction mechanism between the material surface and nitrogen. At high temperatures, the binding energy and reactivity of nitrogen molecules with metal surface atoms determine whether a nitride layer will form or affect cutting quality. By controlling nitrogen flow rate, pressure, and cutting process parameters, this process can be effectively regulated. Relevant studies show that in aluminum alloy laser cutting, nitrogen-assisted cutting can reduce surface roughness by about 25% and improve cutting precision by about 15%.
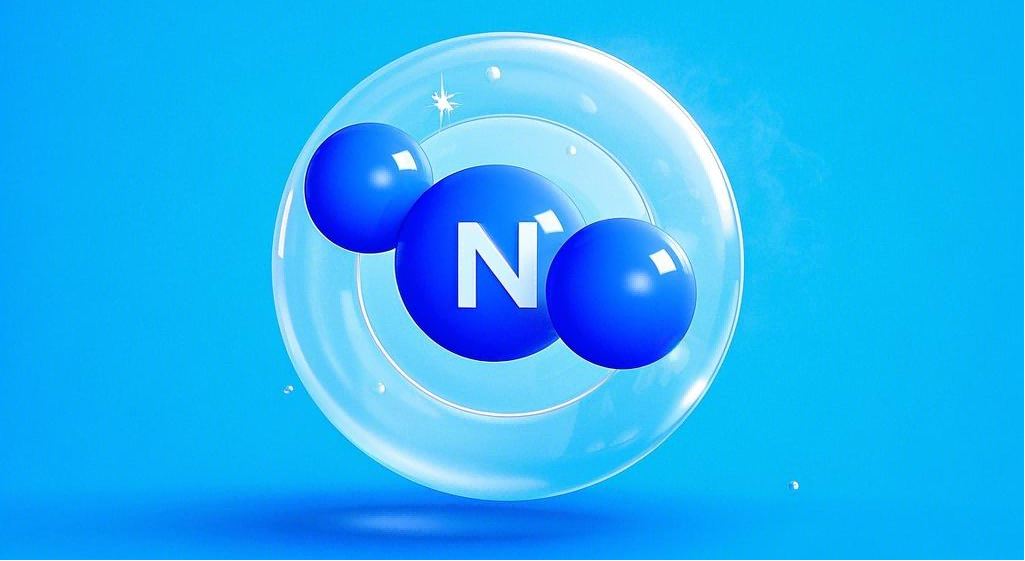
3. Application Parameters and Process Optimization of Nitrogen in Laser Cutting
(1) Impact of Nitrogen Pressure and Flow Rate
Nitrogen pressure and flow rate are critical parameters affecting laser cutting quality and efficiency. If the pressure is too low, it cannot effectively blow away slag, leading to reduced cutting surface quality and slower cutting speeds. If the pressure is too high, it may exert excessive force on the cutting area, causing material deformation or even disrupting the laser beam, affecting cutting results. In terms of flow rate, insufficient flow can lead to inadequate slag removal, causing slag to accumulate in the cutting seam and hindering the cutting process. Excessive flow, on the other hand, can waste gas and increase production costs. According to fluid dynamics principles, the flow state of nitrogen in the cutting area can be described by the Reynolds number :
Re=ρvd/μ
(where ρ is fluid density, v is flow velocity, d is characteristic dimension, and μ is dynamic viscosity).
An appropriate Re range corresponds to effective slag removal and cooling. By adjusting pressure and flow rate, the flow velocity v can be controlled, thereby regulating the flow state of nitrogen. Therefore, it is necessary to precisely adjust nitrogen pressure and flow rate based on factors such as material thickness, type, and laser power.
(2) Matching Cutting Speed with Nitrogen Parameters
There is a close relationship between cutting speed and nitrogen parameters. At a given laser power, if the cutting speed is too fast, nitrogen may not have enough time to completely blow away the slag, resulting in a rough cutting surface and residual slag. If the cutting speed is too slow, the material may overheat, creating a larger heat-affected zone and affecting material properties. To achieve optimal cutting results, it is necessary to adjust the cutting speed based on nitrogen pressure and flow rate. Through experiments and empirical data, a matching relationship table between cutting speed and nitrogen parameters for different materials and thicknesses can be established, providing a reference for actual production.
For example, when cutting 3mm thick carbon steel with a nitrogen pressure of 0.8 MPa and a flow rate of 20 L/min, the appropriate cutting speed may be around 1.5 m/min. By continuously optimizing the matching relationship between these parameters, production efficiency and product quality can be improved. This matching process can be aided by numerical simulation methods, such as finite element analysis software, to couple the temperature field, stress field, and flow field in the laser cutting process, providing an in-depth study of the impact of cutting speed and nitrogen parameters on cutting quality.
(3) Synergistic Effect of Laser Power and Nitrogen Assistance
Laser power determines the energy input for cutting materials, while nitrogen assistance affects slag removal, oxidation prevention, and other effects during the cutting process. At low laser power, nitrogen’s primary role is to assist in slag removal, preventing slag from affecting the cutting surface. As laser power increases, more heat is generated during cutting, and nitrogen must not only remove slag but also provide better cooling and oxidation prevention. Therefore, in practical applications, nitrogen parameters and usage must be adjusted based on laser power. For high-power laser cutting, higher nitrogen pressure and flow rates may be required to ensure good cutting quality under high-temperature, high-energy conditions.
From an energy conservation and transfer perspective, the energy provided by laser power is used to melt and vaporize the material, while the energy carried away by nitrogen affects the temperature distribution and heat-affected zone size in the cutting area. The energy balance between these two factors plays a key role in cutting quality and efficiency.
4. Key Roles of Nitrogen Generators and Nitrogen Compressors in Laser Cutting
(1) Nitrogen Generators: Ensuring Stable Nitrogen Supply
A.Core Position
Nitrogen generators are key equipment for obtaining nitrogen in laser cutting, and their performance directly determines nitrogen output, purity, and production costs. High-quality nitrogen generators provide stable, high-quality nitrogen supply for laser cutting, forming the foundation for ensuring cutting effectiveness.
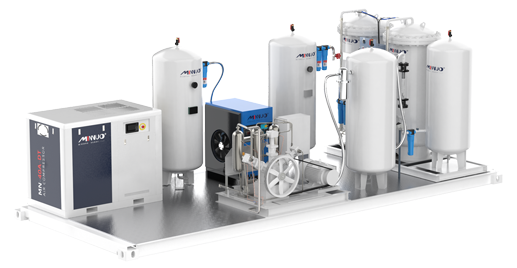
B.Working Principles of Two Main Nitrogen Generation Technologies
- Pressure Swing Adsorption (PSA) Nitrogen Generation
PSA nitrogen generators use the differential adsorption capacity of adsorbents for different gases to achieve nitrogen separation. Common adsorbents like carbon molecular sieves have strong adsorption capacities for oxygen, carbon dioxide, and other impurities under certain pressures, while weakly adsorbing nitrogen, thereby enriching nitrogen. This process is based on adsorption isotherm theories such as the Langmuir isotherm :
q = qmKp/(1 + Kp)
(where q is adsorption capacity, qm is monolayer saturation capacity, K is adsorption equilibrium constant, and p is gas pressure) and the Freundlich isotherm:
q = KFp1/n
(where KF and n are empirical constants), which describe the relationship between adsorbent adsorption capacity and pressure for different gases.
By controlling pressure changes, selective adsorption and separation of gases are achieved. Advanced PSA nitrogen generators use automated control technology to precisely manage adsorption time, pressure, and other parameters, improving nitrogen generation efficiency and purity. PSA technology can produce high-purity nitrogen, typically reaching 99.9% or higher, with special processes achieving 99.999%, meeting the stringent requirements for high-purity nitrogen in laser cutting and providing reliable nitrogen supply for high-end precision laser cutting operations.
- Membrane Separation Nitrogen Generation
Membrane nitrogen generators use special polymer membrane materials to separate gases based on their different permeation rates. Under pressure, air passes through the membrane module, and smaller molecules like oxygen and water vapor permeate more easily than nitrogen, resulting in nitrogen-enriched gas on the other side. The membrane separation process follows the solution-diffusion model, where gas permeation rates depend on solubility and diffusion coefficients in the membrane material. By optimizing the chemical structure and physical properties of the membrane material, gas solubility and diffusion coefficients can be controlled, improving nitrogen separation efficiency. Membrane separation technology offers advantages such as simple equipment structure, compact size, and fast startup, but its nitrogen purity is relatively lower.
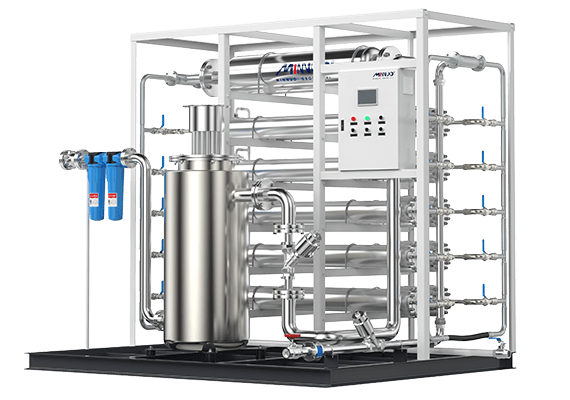
C.Factors Affecting Nitrogen Generator Performance
- Equipment Quality
The manufacturing process and materials of nitrogen generators directly impact their performance and stability. High-quality equipment uses superior adsorbents and membrane materials, along with advanced manufacturing techniques, ensuring long-term stable gas separation and reducing equipment failures and maintenance costs. High-precision machining processes for adsorption towers and membrane modules ensure internal structural accuracy, improving gas separation efficiency. For example, the uniformity of gas flow distribution inside the adsorption tower significantly affects PSA nitrogen generation efficiency. MINNUO optimizes tower internal structure and gas distributor design to ensure more uniform gas contact with the adsorbent, enhancing adsorption efficiency.
- Operating Parameters
Parameters such as adsorption time, pressure, and temperature significantly impact nitrogen generator performance. Properly adjusting these parameters can optimize the nitrogen generation process, improving nitrogen output and purity. In practical operation, experiments and simulations are used to determine the best operating parameters based on the type of nitrogen generator and specific working conditions. Computational fluid dynamics (CFD) simulation technology is employed to study gas flow and separation processes within the nitrogen generator, optimizing operating parameters and enhancing performance. For example, in PSA nitrogen generation, MINNUO uses CFD simulations to analyze the impact of different adsorption times and pressure changes on gas concentration distribution and adsorbent utilization within the adsorption tower, helping determine optimal operating parameters.
(2) Nitrogen Compressors: Key Power for Pressure Boosting
A.Indispensable Pressurization Role
Nitrogen compressors are critical equipment in laser cutting nitrogen application systems, primarily responsible for pressurizing generated nitrogen to the levels required for laser cutting operations. Laser cutting typically requires nitrogen pressure to reach certain levels to meet the cutting needs of different materials and thicknesses. For example, when cutting thicker metal plates, nitrogen pressure must be increased to higher levels to ensure effective slag removal and high-quality cutting. According to the ideal gas law :
PV = nRT
(where P is pressure, V is volume, n is the amount of substance, R is the gas constant, and T is temperature), at constant temperature and substance amount, compressing nitrogen reduces volume, thereby increasing pressure to meet laser cutting requirements.
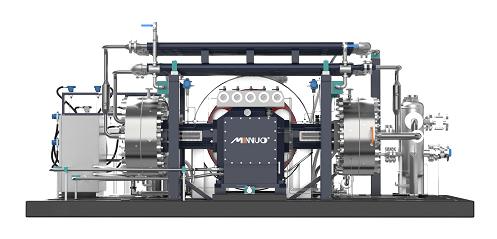
B.Performance Requirements for Compressors
- Stability
High-quality nitrogen compressors must have stable pressurization performance, maintaining consistent pressure output over long periods. In laser cutting, stable pressure ensures consistent cutting results. Excessive pressure fluctuations can lead to unstable cutting surface quality, affecting precision. MINNUO’s advanced pressure control system can monitor and precisely adjust output pressure in real-time, ensuring minimal pressure fluctuations during prolonged operation, guaranteeing efficient and stable laser cutting operations, and improving cutting quality and efficiency. This pressure control process can be achieved through feedback control theory, using pressure sensor signals as feedback, comparing them with set pressure values, and adjusting compressor operating parameters such as speed and valve opening to maintain stable output pressure.
- Adaptability
Laser cutting applications vary widely, with different environmental conditions. Therefore, nitrogen compressors must have good environmental adaptability, operating reliably under different temperatures and humidity levels, reducing equipment failures caused by environmental factors. MINNUO deeply optimizes lubrication and cooling systems, using high-temperature and corrosion-resistant materials, along with efficient cooling devices, ensuring stable operation of nitrogen compressors in various environments, significantly reducing equipment failure rates. For example, in high-temperature environments, optimizing cooling system heat dissipation area and coolant flow ensures that key compressor components remain within safe temperature ranges, ensuring reliable operation.
- Efficiency
To meet the demands of large-scale laser cutting production, nitrogen compressors should have high compression efficiency, processing more nitrogen per unit time, improving production efficiency, and reducing energy consumption. MINNUO optimizes the structural design of nitrogen compressors, using new compression chamber profiles and advanced manufacturing techniques, effectively reducing gas leakage and improving compression efficiency. From a thermodynamic perspective, compression efficiency is related to how closely the compression process approximates isentropic compression. By optimizing compression chamber profiles and manufacturing processes, the compression process more closely approximates isentropic compression, reducing energy loss and improving efficiency. This meets the demands of laser cutting production while lowering energy consumption and operating costs, providing significant economic benefits.
5. Conclusion
By rationally selecting and optimizing nitrogen application parameters, and equipping high-performance nitrogen generators and compressors, the quality and efficiency of laser cutting can be significantly improved, expanding the range of cuttable materials.
Clearly, MINNUO will become your most reliable partner. Contact us today!