In contemporary industrial production, air compressors are extensively applied across diverse sectors. However, the issue of air compressor oil leakage frequently challenges the stable operation of equipment and the improvement of production efficiency. Thus, a comprehensive analysis of the common causes of air compressor oil leakage and the exploration of effective solutions are of great significance for ensuring the reliable operation of air compressors, reducing production costs, and enhancing the safety and stability of production processes.
The problem of air compressor oil leakage can be addressed through regular maintenance, prompt replacement of damaged components, optimization of the oil circuit system, and precise pressure control. First, regularly inspect components like seals, oil pipes, and oil return check valves. Replace any damaged components immediately and ensure correct installation. Second, maintain the lubricating oil pressure within the normal range to avoid excessive pressure. Also, clear the oil return pipeline to prevent blockages. Finally, rationally adjust the operating load of the air compressor to ensure stable operation under rated conditions.
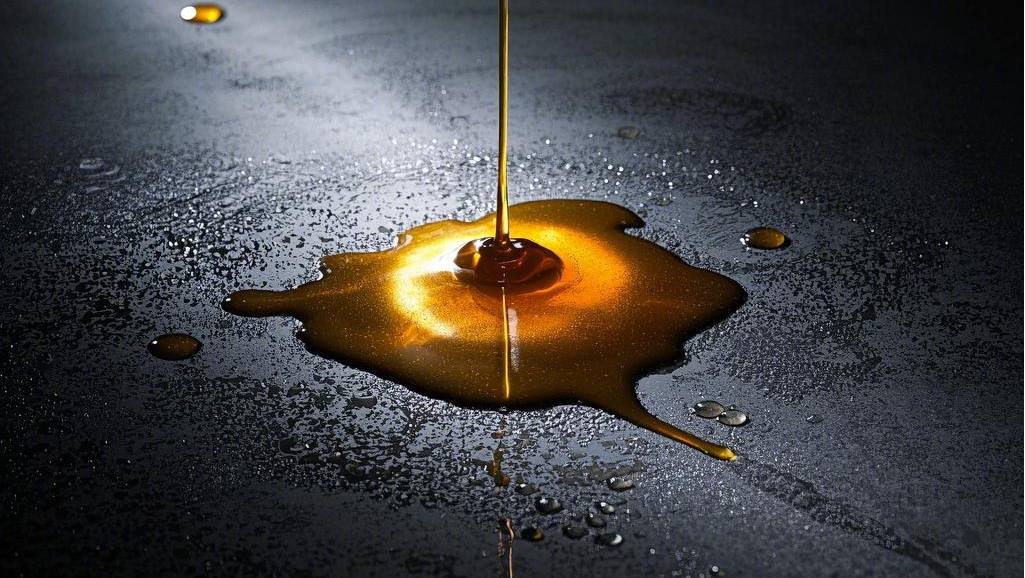
I. Common Causes of Air Compressor Oil Leakage
(1) Seal Damage
1. Aging
During the long – term operation of air compressors under complex working conditions, seals are continuously affected by high temperatures, high pressures, and the chemical environment of lubricating oil. Taking rubber – based sealing materials as an example, according to the thermal degradation theory of polymer materials, high temperatures accelerate the random breakage of molecular chains, leading to a significant decline in the physical properties of the material. In a 120°C high – temperature environment, the thermal motion of the molecular chains in rubber seals intensifies, and the rate of cross link bond breakage increases substantially. Experimental verification shows that its service life will be shortened by more than 50%.
At the same time, high pressures cause stress concentration within the material, disrupting intermolecular interactions. Additive components in lubricating oil, such as antioxidants and anti wear agents, may react chemically with the rubber, resulting in swelling or chemical corrosion. Over time, the seal gradually loses its elasticity, the Shore hardness increases significantly, the microscopic fit of the sealing interface deteriorates, and leakage channels gradually form, ultimately causing oil leakage.
2. Improper Installation
During seal installation, if the assembly process requirements based on the principles of mechanical assembly are not strictly followed, for example, if the installation position deviation of the seal exceeds the tolerance range, according to the theory of elasticity, the seal will bear uneven stress distribution in its initial state, creating a potential for damage. Uneven application of extrusion force during assembly will cause local over – deformation of the seal, reducing its sealing performance.
Moreover, the high – frequency vibrations and sudden impact loads generated during air compressor operation subject the seal to alternating stress, as per the theory of dynamics. When the alternating stress exceeds the fatigue limit of the material, the seal will experience local tearing and deformation, thus compromising its sealing performance. Experiments demonstrate that when the installation deviation of the seal reaches 0.5mm, its sealing performance will decrease by over 30% due to the stress concentration effect.
(2) Loosening of Oil Circuit System Components
The various components of an air compressor are connected by bolts. Long – term mechanical vibrations, temperature fluctuations, and stress impacts from equipment startup and shutdown are the main factors leading to a reduction in bolt pre – tightening force.
Mechanical vibrations cause small relative displacements of the bolts. Based on the principles of tribology, these small displacements gradually deplete the bolt’s pre – tightening force. Temperature changes cause thermal expansion and contraction of materials, altering the stress state between connected components and further weakening the bolt’s pre – tightening force. The impact loads generated during equipment startup and shutdown subject the bolts to instantaneous high stresses, accelerating the attenuation of the pre – tightening force. Once the bolts become loose, gaps form at the interfaces, and lubricating oil leaks along these gaps under the influence of pressure differentials and gravity.
(3) Excessive Pressure
During air compressor operation, excessive lubricating oil pressure may be caused by malfunctions in the pressure regulating valve of the lubrication system or abnormal output of the oil pump.
Malfunctions in the pressure regulating valve can be due to factors like valve core jamming or spring fatigue, preventing it from accurately adjusting the pressure according to system requirements. Abnormal output of the oil pump may be caused by pump wear or internal leakage, resulting in the actual output flow and pressure of the oil pump exceeding the designed range.
Excessive oil pressure subjects the seals to pressures far beyond the design specifications. According to Bernoulli’s equation in fluid mechanics and the strength theory in solid mechanics, excessive pressure increases the shear stress and normal stress on the seals. When these stresses exceed the yield strength and fatigue limit of the seal material, seal wear, deformation, and damage occur, ultimately leading to oil leakage. This is especially true for air compressors operating under high – pressure conditions, where seals are more prone to failure due to excessive pressure.
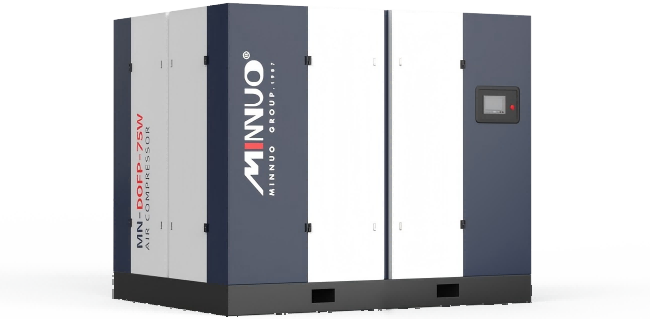
(4) Oil Pipe Damage
1. Aging and Wear
Oil pipes are exposed to high – temperature and humid environments for long periods and are eroded by the flow of oil. Rubber or metal oil pipes will gradually age and wear. For rubber oil pipes, high temperatures accelerate the oxidation and aging process of rubber, while humid environments trigger hydrolysis reactions, and the scouring of oil leads to surface wear and fatigue. In high – temperature and high – humidity environments, the oxidation and hydrolysis rates of rubber molecular chains accelerate. Relevant research indicates that its aging rate can increase by 3 to 5 times. Metal oil pipes may experience internal corrosion and thinning as a result of electrochemical corrosion reactions between water, acidic substances, etc., in the oil and the metal. Over time, the wall thickness of the pipe gradually decreases, eventually leading to pipe rupture and oil leakage.
2. Improper Installation
If the oil pipe is over bent, stretched, or not fixed firmly during installation, it will be subjected to additional stress due to vibrations and displacements during equipment operation. According to the theory of material mechanics, over bending causes the inner side of the oil pipe to be compressed and the outer side to be stretched, resulting in stress concentration. Stretching places the oil pipe in a tensile stress state, reducing its load – bearing capacity. Insecure fixation causes the oil pipe to experience relative displacements during vibrations, exacerbating wear. Experiments show that when the over – bending angle of the oil pipe exceeds 30°, its local stress concentration coefficient increases significantly, and its service life is shortened by more than 50%.
(5) Cooler Damage
The cooler of an air compressor is responsible for cooling the compressed air and dissipating heat from the lubricating oil. When the cooler is damaged, cracked, or the seal at the interface fails, lubricating oil will leak from these vulnerable areas. Corrosion – induced perforation of the heat exchange tubes inside the cooler occurs due to chemical reactions between corrosive substances in the cooling medium and the heat exchange tube material. For example, in cooling water containing chloride ions, stainless – steel heat exchange tubes may experience pitting corrosion. According to the principles of heat exchange, a decline in cooler performance leads to an increase in oil temperature. Elevated oil temperatures accelerate the oxidation and deterioration of the lubricating oil, reducing its lubricating properties and expediting the aging and damage of seals. The aging and damage of the sealing gaskets at the interfaces are mainly caused by the long – term effects of high temperatures, pressures, and chemical media, leading to the degradation of material properties and the loss of sealing capabilities, thus causing lubricating oil leakage.
(6) High Gas Consumption and Overload Low Pressure Operation
When the exhaust pressure of an air compressor does not reach the rated working pressure and the compressor operates under high – load conditions for an extended time, the gas and oil circuits within the compressor become disrupted. To maintain operation, the oil pump increases the oil supply, resulting in higher oil consumption. According to the performance curve of the compressor and the law of conservation of energy, during overload low pressure operation, the volumetric efficiency of the compressor decreases. To meet the gas demand, the oil pump must supply more lubricating oil to maintain lubrication and sealing. Excessive oil in the system cannot circulate properly, thus causing oil leakage. Research shows that when an air compressor operates at 10% overload, its oil consumption increases by more than 20% due to the complex thermodynamics and fluid mechanics factors involved.
(7) Blockage of the Oil Return Pipeline
The presence of foreign objects in the oil return pipeline, such as metal debris, sludge, and impurities, can cause pipeline blockages. This prevents the oil that has condensed at the bottom of the oil separator from flowing back to the compressor head smoothly. As the oil level at the bottom of the oil separator rises continuously, it eventually exceeds the sealing range, leading to oil leakage. According to the principles of fluid mechanics, pipeline blockages increase the oil return resistance. When the resistance exceeds the pumping capacity of the oil pump, poor oil return occurs. The formation of sludge is mainly due to the oxidation and polymerization reactions of lubricating oil under high – temperature, high – pressure, and metal – catalyzed conditions. The resulting macromolecular substances gradually aggregate to form viscous deposits. Metal debris may come from worn – out components within the equipment, such as bearings and gears.
(8) Damage to the Oil Return Check Valve
The oil return check valve is designed to ensure the unidirectional flow of oil from the oil separator tank back to the compressor head. If the oil return check valve is damaged, for example, if the valve core is worn or the spring fails, the pressure in the oil separator tank will force a large amount of oil to flow back into the oil separator through the oil return pipe, causing an excessive accumulation of oil in the oil separator and resulting in oil leakage. Experimental data shows that when the leakage rate of the oil return check valve reaches 10%, it significantly impacts the air compressor’s oil return system. The wear of the valve core is mainly caused by the long – term scouring of the oil and the abrasion of impurities. The failure of the spring may be due to long – term exposure to alternating loads, causing material fatigue.
(9) Malfunction of the Minimum Pressure Valve
The minimum pressure valve in the air compressor system serves to maintain system pressure and ensure efficient oil – gas separation. When the minimum pressure valve malfunctions, such as valve core jamming or poor sealing, it causes abnormal fluctuations in system pressure, deteriorates the oil – gas separation effect, and results in excessive oil being discharged with the compressed air or leaking within the system. According to the principles of gas dynamics, the malfunction of the minimum pressure valve affects the airflow distribution and pressure balance within the air compressor, altering the flow rate and pressure of the oil – gas mixture and thus degrading the oil – gas separation effect. Valve core jamming may be caused by factors such as impurity intrusion or poor lubrication, while poor sealing may be due to wear and deformation of the sealing surface.
(10) Non – compliant Design of the Oil – Gas Separation Tank
If the design of the oil – gas separation tank is unreasonable, such as improper internal structure layout or inappropriate filter element selection, it can lead to an over – burdened oil separator with insufficient processing capacity. A large amount of oil cannot be effectively separated, either being discharged with the compressed air or accumulating excessively in the tank and leaking from the seals. Through numerical simulations and experimental studies, it has been found that an inappropriate design of the oil – gas separation tank can reduce the oil – separation efficiency by 20% to 30%. Improper internal structure layout may cause the flow field of the oil – gas mixture to become disordered, impeding the coagulation and separation of oil droplets. Inappropriate filter element selection may fail to meet the requirements for filtration accuracy and flow rate, allowing oil to penetrate the filter element and be discharged with the compressed air.
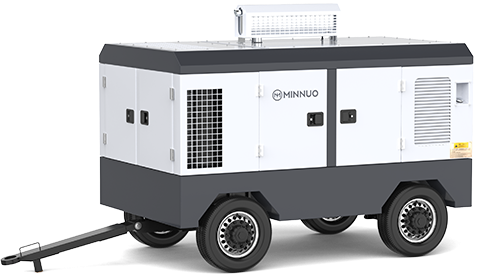
II. Solutions to Air Compressor Oil Leakage
(1) Regular Maintenance
Establish a comprehensive regular maintenance regime in line with the requirements specified in the equipment operation manual, setting a fixed maintenance cycle. During each maintenance, conduct a thorough inspection of critical components, including seals, bolts, oil pipes, and coolers. Document in detail the wear and aging conditions of components to provide a basis for subsequent repairs and replacements. Employ advanced non – destructive testing techniques, such as ultrasonic testing, which uses the propagation characteristics of ultrasonic waves in different media to detect internal defects in components, and infrared thermography, which analyzes the surface temperature distribution of components to identify potential fault risks.
(2) Replacement of Damaged Components
1. Seals
Upon discovery of aged, damaged, or improperly installed seals, replace them immediately. Before replacement, accurately determine the model and specification parameters of the seals by referring to the technical documentation, product samples of the air compressor equipment, and seal markings. These parameters include the inner diameter, outer diameter, thickness, sealing type (such as lip – type seal, O – ring seal, etc.), and the applicable working medium, temperature, and pressure range. During installation, strictly follow the installation process specifications, use specialized tools to ensure the smooth and accurate installation of the seals, avoid twisting and scratching, apply an appropriate amount of lubricating grease compatible with the lubricating oil, and tighten the connecting bolts or nuts to the specified torque.
2. Oil Pipes
For oil pipes that are aged, worn, or damaged due to improper installation, select suitable pipes for replacement based on their material, specifications, and working pressure. When installing a new oil pipe, ensure a rational pipeline routing, avoiding unnecessary bends, stretches, and crossovers. Adopt the correct connection method (such as welding, flange connection, ferrule connection, etc.) and follow the connection process requirements carefully. After installation, conduct a pressure test to check for leaks.
3. Oil Return Check Valve and Minimum Pressure Valve
If the oil return check valve or the minimum pressure valve malfunctions, disassemble and inspect components such as the valve core and spring. Replace any worn – out or damaged components with new ones of the same specification and model in a timely manner to ensure the proper functioning of the valve. Implement intelligent detection technologies, such as pressure sensors and flow sensors, to monitor the valve’s working status in real – time. Develop a valve fault diagnosis model and use machine – learning algorithms to analyze the sensor data, enabling the timely detection of fault risks. For example, by monitoring the pressure difference and flow rate changes at the inlet and outlet of the valve, it is possible to determine whether the valve is experiencing issues such as leakage or jamming.
(3) Resolution of Pressure and Oil Circuit Issues
1. Pressure Regulation
To address the problem of excessive lubricating oil pressure, inspect the pressure regulating valve of the lubrication system. Clean or replace the faulty pressure regulating valve and adjust the output of the oil pump to restore the lubricating oil pressure to the normal range. At the same time, regularly calibrate the pressure sensor to ensure accurate pressure monitoring. Adopt advanced pressure control technologies, such as proportional pressure regulating valves, which can precisely control the valve opening by adjusting the input current or voltage, enabling continuous regulation of the lubricating oil pressure. Also, variable frequency speed regulation technology can be used to adjust the output flow and pressure of the oil pump by changing the speed of the oil – pump motor, achieving precise control of the lubricating oil pressure.
2. Clearing of the Oil Return Pipeline
When the oil return pipeline is blocked, disassemble the pipeline and use high – pressure cleaning agents, chemical solvents, or specialized clearing tools to remove foreign objects and sludge, restoring pipeline flow. During reinstallation, ensure a tight pipeline connection to prevent re – blockage. Utilize advanced equipment such as pipeline – cleaning robots, which can be remotely controlled to move within the pipeline for efficient cleaning operations, improving the cleaning efficiency and quality of the oil return pipeline.
(4) Optimization of Operation Management
1. Rational Load Operation
In actual industrial production, gas demand fluctuates according to production rhythms and process changes. Therefore, it is crucial to adjust the operating parameters of the air compressor rationally according to the actual gas demand. Overload low pressure operation not only reduces the volumetric efficiency of the air compressor but also results in abnormal lubricating oil consumption and an increased risk of oil leakage. MINNUO, with its highly professional engineering team, can design the optimal gas – utilization plan for you, adjust the operating parameters, and ensure the stable operation of the air compressor near the rated conditions.
2. Cooler Maintenance
Regularly clean the cooler to remove internal dirt and impurities, ensuring good heat – dissipation performance. Check the sealing performance of the cooler and promptly replace any aged or damaged sealing gaskets to prevent lubricating oil leakage. MINNUO uses enhanced heat – transfer technologies to improve the heat – transfer capacity of the cooling medium and enhance the heat – dissipation efficiency of the cooler. Thus, customers who purchase our products need not worry about quality issues.
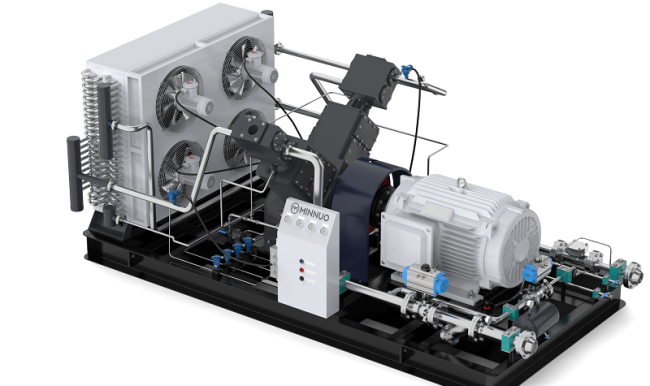
III. Conclusion
In summary, air compressor oil leakage is caused by the combined action of multiple factors. In practical operations, enterprises should attach great importance to the maintenance and management of air compressors and strictly comply with relevant specifications and requirements to fully utilize the important role of air compressors in production.
If you wish to obtain the most professional consulting services regarding compressor equipment, please visit the official MINNUO website.