We know that compressors are indispensable and crucial equipment in the industrial sector, widely used in various industries. Compressors come in different types, each with unique advantages and characteristics in terms of performance, efficiency, and applicability. This article will provide a detailed introduction to the main classifications of compressors to help you better understand the working principles and applications of different compressor types.
There are various ways to classify compressors: by working principle (volumetric type, including reciprocating and rotary; and fluid dynamic type, including turbine and jet), by compression action (single-acting, double-acting, multi-cylinder single-acting, and multi-cylinder double-acting), by discharge pressure (low pressure, medium pressure, high pressure, and ultra-high pressure), by displacement (micro, small, medium, and large), by cylinder arrangement (vertical, horizontal, angular, star-shaped), and by lubrication type (oil-lubricated and oil-free lubrication).They are classified by medium, such as oxygen compressors, hydrogen compressors, and so on.
I. Classification Based on Working Principle
Compressors are mainly divided into two categories: volumetric compressors and fluid dynamic compressors.
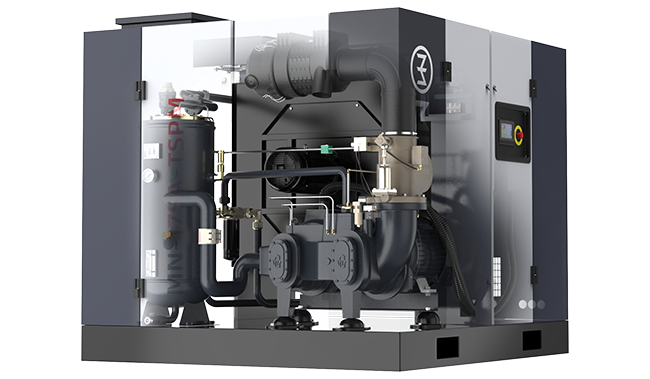
(1) Volumetric Compressors
1.Reciprocating Type:
- Piston Type: This is a common compressor type that compresses gas through the reciprocating motion of a piston inside the cylinder. It has a relatively simple structure, and its working principle is easy to understand. It is widely used in small refrigeration equipment, air compressors, etc.
- Diaphragm Type: This compressor uses a diaphragm that reciprocates inside the cylinder to compress and deliver gas. It has the advantages of good sealing, and the compressed gas is not contaminated by lubricating oil, making it suitable for applications requiring high gas purity, such as in food and pharmaceutical industries.
- Inclined Plate Type: This type uses the rotation of an inclined plate to drive a piston in a reciprocating motion. It is compact and small in size, commonly found in automotive air conditioning compressors.
- Free Piston Type: The piston’s motion is not restricted by mechanical structures such as a crankshaft, offering flexibility and efficiency. It has unique applications in specialized power systems and compressors.
2.Rotary Type:
- Screw Type: Comprised of a pair of intermeshing screws, this type compresses gas through the rotation of the screws. It is highly efficient, reliable, and provides uniform discharge, widely used in large refrigeration systems, air compressors, and more.
- Roots Type: This type compresses gas through the rotation of two rotors, offering a wide flow range and stable pressure. It is commonly used in wastewater treatment, pneumatic conveying, etc.
- Liquid Ring Type: This type uses a liquid ring to compress gas. It features a simple structure and oil-free lubrication, making it suitable for compressing flammable or explosive gases, with significant applications in the chemical industry.
- Sliding Vane Type: This compressor compresses gas by altering the cylinder volume through the sliding of vanes inside the rotor slots. It is commonly used in small refrigeration equipment and air compressors.
- Rotary Piston Type: It compresses gas through the rotary motion of a piston, playing a role in specific devices and systems.
(2) Fluid Dynamic Compressors
1.Turbine Type:
- Centrifugal Type: This type uses a high-speed rotating impeller to impart kinetic energy to the gas, which is then converted into pressure energy via a diffuser. It has large flow capacity and compact structure, widely used in large air compression and refrigeration systems.
- Axial Flow Type: Gas enters the compressor axially, and its pressure increases through the interaction of impellers and stators. It is used in large ventilation, air conditioning systems, and gas turbines.
- Mixed Flow Type: Combining the characteristics of both centrifugal and axial flow types, the gas moves both axially and radially, offering better performance in specific operating conditions.
- Jet Type: This type uses a high-speed jet of fluid to entrain and compress gas. It has a simple structure but relatively low efficiency, commonly used in small, specialized gas compression applications.
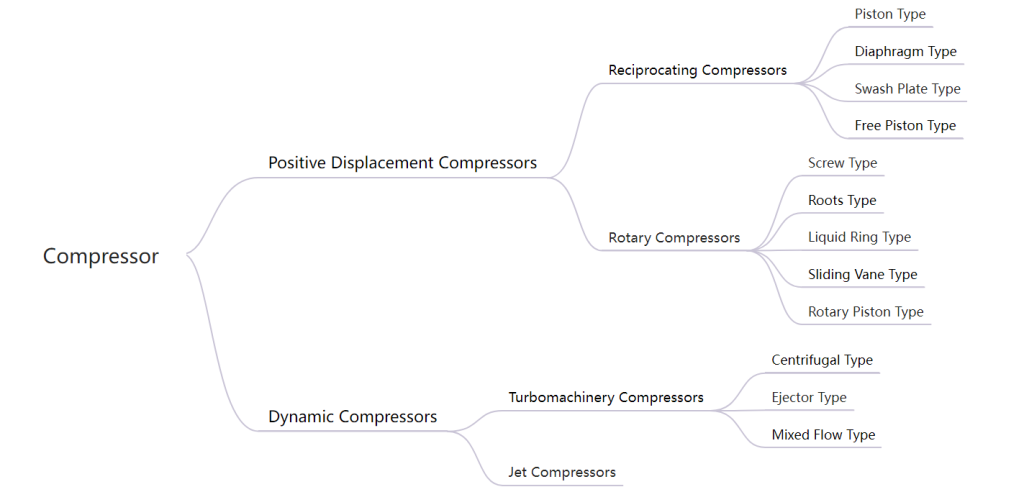
II. Classification Based on Compression Action
(1) Single-Acting Compressors
In these compressors, gas is compressed only on one side of the piston, also known as a single-acting compressor. During each cycle, the piston completes one intake, compression, and exhaust process. These compressors have a simple structure, fewer components, and lower manufacturing costs, but the gas flow and pressure fluctuate due to the intermittent working process. They are suitable for small applications, such as compressing small amounts of gas in laboratories or providing air to simple pneumatic tools.
(2) Double-Acting Compressors
In these compressors, gas is compressed on both sides of the piston, also known as a double-acting or multi-acting compressor. Compared to single-acting compressors, double-acting compressors complete two intake, compression, and exhaust processes within a single piston stroke, providing more stable gas flow and pressure and higher output power. They are widely used in industrial production, such as in small gas filling stations or workshops requiring stable compressed air.
(3) Multi-Cylinder Single-Acting Compressors
These compressors use a single side of the piston for compression but have multiple cylinders. The collaboration of multiple cylinders can increase gas compression capacity and, through proper cylinder arrangement and timing, can reduce fluctuations in gas flow and pressure. They are commonly used in industries like chemicals and pharmaceuticals, where stable compressed gas is needed for multiple reaction vessels.
(4) Multi-Cylinder Double-Acting Compressors
These compressors compress gas on both sides of the piston and have multiple cylinders. They combine the advantages of double-acting and multi-cylinder compressors, offering higher compression efficiency, more stable gas output, and larger discharge capacity. These compressors are suitable for large-scale industrial production requiring high-pressure gas. They are often used in large steel plants, oil refineries, and other enterprises.
Classification | Definition |
Single-Acting Compressor | Compression occurs on only one side of the piston, also known as a single-action compressor. |
Double-Acting Compressor | Compression occurs on both sides of the piston, also known as a double-action or multi-action compressor. |
Multi-Cylinder Single-Acting Compressor | A compressor that uses one side of the piston for compression but has multiple cylinders. |
Multi-Cylinder Double-Acting Compressor | A compressor that uses both sides of the piston for compression and has multiple cylinders. |
III. Classification Based on Discharge Pressure
(1) Low-Pressure Compressors
These compressors have a discharge pressure between 3–10 bar gauge. They are typically used in applications where the pressure requirements are not high, such as providing air to pneumatic tools or small ventilation systems. Their structure is simple, and they are cost-effective, easy to operate and maintain.
(2) Medium-Pressure Compressors
These compressors have a discharge pressure between 10–100 bar gauge. Medium-pressure compressors are widely used in industrial production, such as providing gas pressure for medium-pressure reactions in chemical synthesis or supplying compressed air for automotive spray painting. They require sufficient strength and sealing to ensure safe and stable operation at medium pressure.
(3) High-Pressure Compressors
These compressors have a discharge pressure between 100–1000 bar gauge. High-pressure compressors are mainly used in fields requiring high gas pressures, such as high-pressure storage and transportation of natural gas, or in high-pressure air storage systems. They require high-strength materials and advanced sealing technologies to withstand the forces from high-pressure gas and prevent leaks.
(4) Ultra-High-Pressure Compressors
These compressors have a discharge pressure above 1000 bar gauge. Ultra-high-pressure compressors are premium products in the compressor field, used for extreme applications such as ultra-high-pressure experimental research, deep-sea diving gas filling, and missile launch systems. They are highly technical, expensive to research and manufacture, and represent the cutting-edge of compressor technology.
Classification | Exhaust Final Pressure |
Low-Pressure Compressor | 3-10 bar gauge pressure |
Medium-Pressure Compressor | 10-100 bar gauge pressure |
High-Pressure Compressor | 100-1000 bar gauge pressure |
Ultra-High-Pressure Compressor | Above 1000 bar gauge pressure |
IV. Classification Based on Displacement
(1) Micro Compressors
These compressors have a displacement of less than 1 m³/min. They are compact and portable, often powered by electricity. Micro compressors are used in situations requiring extremely small amounts of gas, such as inflating bicycles, balls, or small laboratory gas experiments. They are known for low noise and vibration and are easy to operate.
(2) Small Compressors
These compressors have a displacement of 1–10 m³/min. Small compressors are commonly used in small factories, repair shops, dental clinics, and other locations to provide compressed air for pneumatic equipment like small air pumps and dental treatment devices. They are versatile, flexible, and offer low space and operating cost requirements.
(3) Medium Compressors
These compressors have a displacement of 10–60 m³/min. Medium compressors are used in medium-sized industrial enterprises, such as providing air for jet looms in textile factories or pneumatic conveying in food processing plants. They offer stable gas flow to meet compressed gas needs in moderately scaled production processes.
(4) Large Compressors
These compressors have a displacement greater than 60 m³/min. Large compressors are mainly used in large industrial projects, such as blast furnaces in steel plants and gas transportation in large petrochemical enterprises. These applications require large volumes of high-pressure gas to maintain continuous production processes.
Classification | Discharge Volume |
Miniature Compressor | < 1 m³/min |
Small Compressor | 1-10 m³/min |
Medium Compressor | 10-60 m³/min |
Large Compressor | > 60 m³/min |
V. Classification by Structural Form
(1) Vertical Compressors (Z)
Vertical compressors have cylinder centerlines that are perpendicular to the ground. This design occupies less floor space and is compact, making it suitable for small and medium-sized businesses or areas with limited space. In small machining workshops or laboratories, vertical compressors can be conveniently installed in corners or against walls to provide compressed air for equipment. Due to their structural characteristics, the vibrations during operation are relatively low, which helps improve the stability and lifespan of the equipment.
(2) Horizontal Compressors (P)
Horizontal compressors have cylinder centerlines that are parallel to the ground. These compressors are typically used in small high-pressure applications, such as small high-pressure gas filling stations or laboratory equipment requiring high pressure but relatively low flow. The horizontal structure makes installation and maintenance easier, and under high-pressure conditions, their structural strength and stability are well ensured.
(3) Angled Compressors (L, S)
Angled compressors include various configurations, such as L-shaped and S-shaped, with cylinder centerlines arranged at specific angles. This structural form combines some of the advantages of vertical and horizontal compressors and is widely used in small and medium-sized businesses. For instance, in small chemical factories, angled compressors can be flexibly arranged according to the actual production space, while still meeting the general requirements for compressed gas in production processes.
(4) Star Compressors (T, V, W, X)
Star compressors have cylinders arranged in a star pattern, which offers a compact structure and good balance. During operation, the forces acting on each cylinder partially cancel each other out, reducing vibration and noise. They are suitable for small and medium-sized applications, such as small pharmaceutical or electronics factories, providing a stable and reliable air source for pneumatic equipment used in production processes.
(5) Symmetrical Balanced Compressors (H, M, D)
The design of symmetrical balanced compressors ensures that piston forces are well-balanced, resulting in smooth operation with minimal vibration and noise. These compressors are commonly used in large and medium-sized reciprocating compressors and are widely applied in large production units in industries such as petrochemical, power, and metallurgy. For example, in large refinery hydrogenation cracking units, symmetrical balanced compressors provide a significant amount of high-pressure hydrogen gas to ensure efficient operation of the units.
(6) Opposed Compressors (DZ)
Opposed compressors are primarily used in ultra-high-pressure compression fields. With cylinders arranged in an opposite configuration, they can withstand enormous gas pressure, ensuring the safe and stable operation of the compressor. Opposed compressors play a critical role in extreme applications, such as gas filling for deep-sea diving equipment and ultra-high-pressure physical experiments.
Classification | Structure Code | Application |
Vertical | Z | Used for small and medium-sized compressors |
Horizontal | P | Used for small high-pressure compressors |
Angular | L, S | Small and medium-sized compressors |
Star-shaped | T, V, W, X | Small and medium-sized compressors |
Symmetric Balanced | H, M, D | Widely used, especially in large and medium-sized reciprocating compressors |
Opposed | DZ | Used for ultra-high-pressure compressors |
The following are the cylinder arrangement types for compressors:
- Horizontal: Cylinders are arranged horizontally, simple in structure, easy to install and maintain, commonly used in small high-pressure equipment.
- Vertical: Cylinders are arranged vertically, occupying less floor space, with good stability, suitable for small and medium-sized spaces with limited space.
- V-shaped: Two cylinders are arranged in a V-shape, offering a certain degree of balance. Commonly found in small to medium-sized applications where low vibration and noise are desired.
- W-shaped: Multiple cylinders are arranged in a W-shape, compact structure, with balanced performance. Used in small to medium-sized businesses.
- Fan-shaped (S-shaped): Cylinders are arranged in a fan shape, combining characteristics of angled compressors. Suitable for various locations and process requirements, used in industries like chemicals.
- Star-shaped: Cylinders are arranged in a star configuration, providing good balance and low vibration. Used in small and medium-sized applications requiring stable air sources.
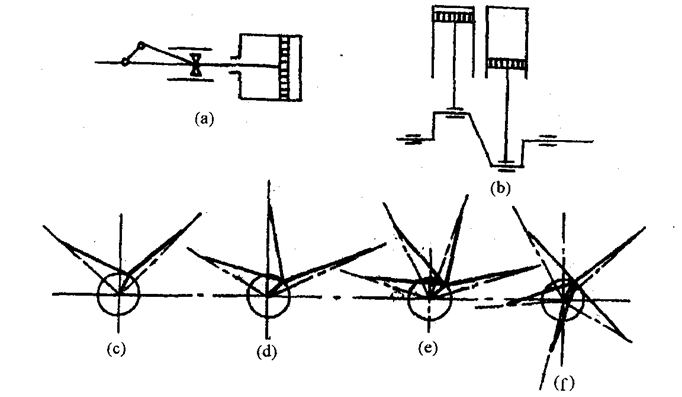
(a) Horizontal; (b) Vertical; (c) V-shaped; (d) W-shaped; (e) Fan-shaped (S-shaped); (f) Star-shaped
VI. Classification by Lubrication Method
(1) Oil-lubricated Compressors
Oil is used to lubricate the moving parts within the compressor, reducing friction and wear while also serving as a sealant and coolant. The oil is forced through an oil pump to the required lubrication points, creating an oil film to ensure normal operation. Oil-lubricated compressors offer good lubrication performance and high reliability, making them suitable for most industrial applications. However, since the lubricating oil comes into contact with the compressed gas, it may cause contamination of the gas. Therefore, in industries with strict purity requirements, such as food, pharmaceuticals, and electronics, oil removal systems are needed, adding to subsequent equipment investment and operating costs.
(2) Oil-free Compressors
To prevent contamination of the compressed gas by lubricating oil, oil-free compressors are designed using special materials and structures that allow lubrication between moving parts without oil. For example, piston rings and cylinder walls are made from self-lubricating materials, such as PTFE, which have low friction coefficients and good wear resistance. Oil-free compressors are mainly used in industries with strict gas quality requirements, such as food processing (to provide clean compressed air for food packaging equipment) and pharmaceuticals (to provide air sources for pneumatic equipment used in drug production). However, oil-free compressors tend to have higher manufacturing costs and, due to the absence of oil for heat dissipation, they require more stringent cooling performance.
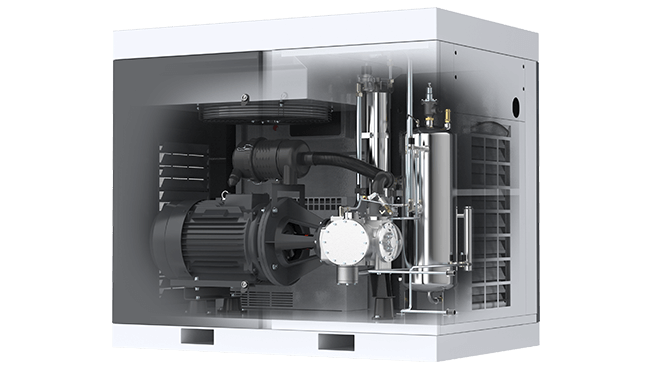
VII. Classification by Medium
(1) Oxygen Compressor(O₂ Compressor)
Oxygen is an oxidizing agent, so oxygen compressors require high standards of material quality and sealing to prevent explosions due to contact with combustible materials. These compressors are widely used in steelmaking, chemical oxidation reactions, and medical oxygen supply. In steelmaking, high-purity oxygen is injected into blast furnaces to improve combustion efficiency and accelerate the smelting process.
(2) Hydrogen Compressor(H₂ Compressor)
Hydrogen is highly flammable and explosive, with a low density. Therefore, hydrogen compressors must be designed with safety and sealing in mind. They are commonly used in hydrogen refueling stations for fuel cell vehicles, and in hydrogenation reactions in the chemical industry, such as hydrocracking in petroleum refining, which improves oil quality.
(3) Compressed Natural Gas Compressor(CNG Compressor)
CNG (Compressed Natural Gas) is primarily methane. CNG compressors are used to compress natural gas to a certain pressure for storage and transport. They are commonly found in natural gas refueling stations, providing fuel for CNG vehicles, and are critical equipment in the automotive use of natural gas.
(4) Biogas Compressor
Biogas mainly consists of methane and carbon dioxide and contains impurities. Biogas compressors must be designed to handle the unique properties of biogas. They are often used in biogas projects to compress the gas for electricity generation, heating, or integration into the natural gas grid.
(5) Nitrogen Compressor(N₂ Compressor )
Nitrogen is chemically stable, and nitrogen compressors are typically used in applications where gas purity and pressure are critical. These include protective gases in chemical production and purging gases in the manufacturing of electronic chips to prevent oxidation.
(6) Liquefied Petroleum Gas Compressor(LPG Compressor)
LPG (Liquefied Petroleum Gas) consists mainly of propane and butane. LPG compressors are used to compress and transport liquefied petroleum gas, commonly used in LPG filling stations, storage facilities, and in industrial processes that rely on LPG as fuel.
(7) Ammonia Compressor(NH₃ Compressor)
Ammonia is corrosive and toxic, so ammonia compressors require materials with good corrosion resistance. They are used in the chemical industry for gas cycling in ammonia synthesis processes and as compression equipment in refrigeration systems using ammonia as a refrigerant.
(8) Carbon Dioxide Compressor(CO₂ Compressor)
Carbon dioxide is a gas at room temperature and pressure. CO2 compressors are used in the capture, storage, and utilization of carbon dioxide. For example, in the food industry, CO2 is compressed and injected into beverages for carbonation, and in oil extraction, CO2 is used for enhanced oil recovery.
(9) Acetylene Compressor(C₂H₂ Compressor)
Acetylene is a flammable and explosive gas, so acetylene compressors are designed with strict explosion-proof measures. They are primarily used in metal welding and cutting, providing stable pressure for acetylene torches.
(10) Mixed Gas Compressor
Mixed gases have diverse compositions, and their compressors must be specially designed based on the specific gases involved. These are commonly used in industries such as chemicals and research, for example, in chemical synthesis reactions, where multiple reaction gases are mixed and compressed in specific ratios to meet the reaction conditions.
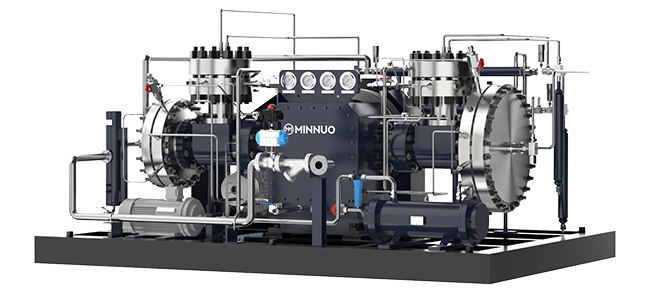
VIII. Conclusion
In conclusion, the classification of compressors not only demonstrates their wide applications across different fields but also highlights the advantages of various compressor types in meeting specific needs. Choosing the appropriate type of compressor is key to ensuring efficient and stable operation of equipment.
MINNUO‘s technical team is always at the forefront of the industry, and the performance and application scope of the compressors we produce will continue to expand, providing more efficient and energy-saving solutions for various industries.