In the complex system of oil field development and production, nitrogen has become an indispensable element in all aspects by virtue of its unique physical and chemical properties. Its application is closely related to core equipment such as nitrogen compressors and nitrogen generators. Next, let’s take a detailed look at the application of nitrogen in oil fields and the use of nitrogen-related equipment.
In oil production, nitrogen flooding enhances recovery rates in low-permeability reservoirs, while gas lift production ensures stable output from deep wells. During workover operations, nitrogen well killing prevents blowouts without contaminating the oil layer, and nitrogen well washing boosts cleaning efficiency and protects the well. Nitrogen is also used for inerting, fire protection, and ensuring safe production. Additionally, nitrogen supports pressure testing for performance evaluation of oil wells and equipment, with nitrogen compressors pressurizing the gas and nitrogen generators providing a stable supply.
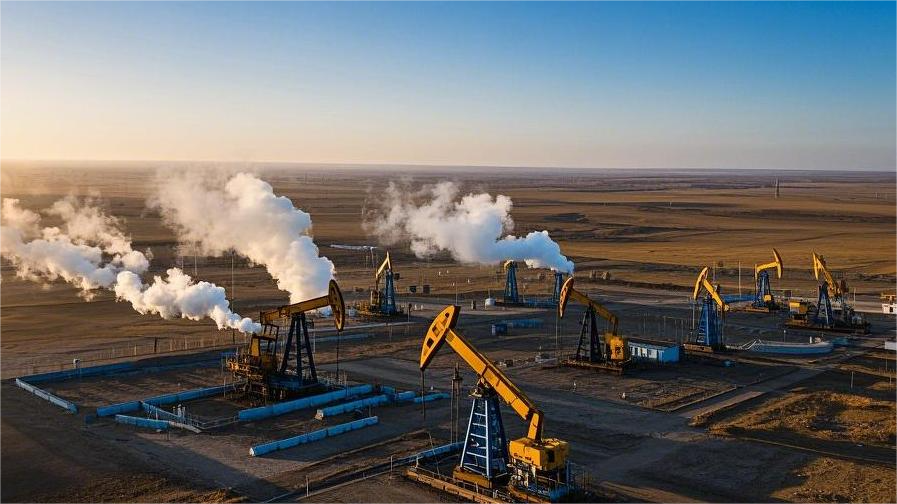
I.The Basis of Nitrogen Application in Oil Fields
(A) The Characteristic Advantages of Nitrogen
Nitrogen is an inert gas with highly stable chemical properties. The energy of the nitrogen-nitrogen triple bond in its molecular structure is as high as 941.69 kJ/mol, making it extremely difficult for nitrogen to react with other substances under normal conditions. In the harsh environment of oil fields, this stability makes it an ideal choice for various operation scenarios. It will neither have a negative impact on the chemical composition and physical properties of crude oil nor ensure the safety of the operation process, effectively avoiding potential safety hazards caused by chemical reactions.
From the perspective of chemical thermodynamics, the Gibbs free energy change of nitrogen participating in the reaction is positive in most oil field working conditions, and the reaction is difficult to occur spontaneously, which fundamentally explains its stability. At the same time, the non-flammability of nitrogen makes it naturally explosion-proof in the inflammable and explosive environment of oil fields, effectively reducing the explosion risk.
(B) The Universality of Application
Nitrogen is widely used in key areas such as oil production, workover, safety guarantee, and pressure testing in oil fields. It can be seen from the macro oil field production layout to the micro oil well operation process. The universality of its application deeply reflects its important position in oil field production and is one of the key factors to maintain the efficient operation of oil fields.
In the process of oil production, various processes involving nitrogen are helpful to improve the recovery rate; in workover operations, nitrogen plays an important role as a well killing and well washing medium; in terms of safety guarantee, nitrogen is used for inerting protection and fire extinguishing to ensure the safety of oil field facilities.In pressure testing, nitrogen is used to assist in the performance evaluation of oil wells and related equipment, ensuring their reliability and stability in actual production environments.
II. The Key Role of Nitrogen in the Oil Production Process
(A) Nitrogen Flooding in Tertiary Oil Recovery
As the oil field development enters the middle and late stages, the reservoir pressure declines and the recovery rate of conventional oil production methods decreases. Nitrogen flooding, as an important technical means of tertiary oil recovery, can effectively supplement the formation energy and increase the reservoir pressure by injecting nitrogen into the oil layer. Nitrogen is immiscible with crude oil and forms a gas drive oil power in the oil layer. By using the expansibility and fluidity of the gas, the residual crude oil in the pores of the oil layer is displaced. In low-permeability reservoirs, nitrogen flooding can increase the recovery rate by 10% – 20%.
Nitrogen flooding can also improve the seepage characteristics of the reservoir. According to Darcy’s law, the injection of nitrogen changes the seepage state of the fluid in the reservoir and increases the fluidity of crude oil. At the same time, from a microscopic perspective, nitrogen molecules are small and can enter tiny pores to displace crude oil, which is of great significance for improving the ultimate recovery rate of oil fields.
(B) Gas Lift Production Helps Oil Wells Produce Stably
For deep wells or wells with low liquid production, gas lift production is an effective production method. Injecting high-pressure nitrogen into the annular space between the tubing and the casing can reduce the density of the liquid in the wellbore and increase the pressure difference between the liquid column and the formation, prompting the crude oil to flow smoothly from the bottom of the well to the ground.
In the process of gas lift production, complex multiphase flow theory is involved. The selection of nitrogen injection volume, injection pressure and gas lift method needs to be accurately optimized according to the specific situation of the oil well. By establishing a mathematical model of the gas lift system and combining the geological parameters and fluid properties of the oil well, the gas lift effect can be maximized and the stable production of the oil well can be ensured.
III. The Application of Nitrogen in Workover and Maintenance Operations
(A) Safe and Reliable Nitrogen Well Killing
When working over a well, the primary task is to balance the pressure in the well to prevent blowouts. Nitrogen is an ideal well killing medium because of its inertness. Compared with traditional well killing fluids, nitrogen well killing has the advantages of not polluting the oil layer and being easy to discharge after well killing.
In actual operation, the pressure control parameters of nitrogen well killing are accurately calculated based on the principle of pressure balance. Factors such as reservoir pressure, wellbore liquid column pressure and pressure fluctuation during the operation process need to be comprehensively considered. By adjusting the nitrogen injection volume and injection pressure, the stable balance of the pressure in the well is achieved, ensuring the safety of the operation personnel and the normal operation of the equipment.
In the nitrogen well killing operation, a stable and high-quality nitrogen supply is the key.
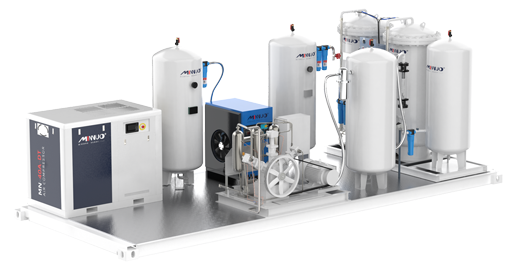
(B) Efficient Nitrogen Well Washing
Nitrogen plays a significant role in well washing operations. High-pressure nitrogen is mixed with water or other well washing fluids to flush the well wall and tubing. Nitrogen enhances the carrying capacity of the well washing fluid and can more effectively remove impurities, deposits and blockages in the well, restoring the production capacity of the oil well.
Research shows that nitrogen well washing can more thoroughly remove pollutants in the well and improve the well washing efficiency compared with conventional well washing methods. This is because the presence of nitrogen changes the rheological properties of the well washing fluid, making its flow in the well more scouring. At the same time, nitrogen well washing has little damage to the oil layer and is beneficial to protecting the long-term production capacity of the oil well.
IV. The Key Contribution of Nitrogen in Oil Field Safety Guarantee
(A) Inerting Protection to Prevent Accidents
In the storage facilities and production areas such as the oil tank area and gathering station in the oil field, there are inflammable and explosive oil-gas mixtures. Filling nitrogen can reduce the oxygen concentration in these areas and make the environment reach an inert state, effectively preventing the occurrence of fire and explosion accidents.
When the oxygen concentration is reduced to below 12%, the combustion and explosion risks of most combustible gases and dusts are significantly reduced. From the perspective of combustion reaction kinetics, after nitrogen dilutes oxygen, the contact probability between combustible substances and oxygen decreases and the reaction rate slows down, thus inhibiting combustion and explosion. The inerting protection effect of nitrogen is an important guarantee for the safe production of oil fields.
(B) Environmentally Friendly Nitrogen Fire Extinguishing
When a fire occurs in an oil field, nitrogen can be used as a fire extinguishing medium. Its inertness and asphyxiation can quickly dilute the oxygen concentration in the combustion area and inhibit the combustion reaction to achieve the purpose of fire extinguishing.
Compared with traditional fire extinguishing methods, nitrogen fire extinguishing is pollution-free and causes little damage to equipment and the environment. At the fire scene, nitrogen can quickly cover the combustion area, isolate the oxygen supply and extinguish the flame. And there is no residue after nitrogen fire extinguishing, which will not cause secondary pollution to the equipment and the environment and is beneficial to the rapid restoration of production after the fire.
V. The Application of Nitrogen in Pressure Testing
(A) The Principle of Nitrogen in Pressure Testing
In the construction and daily maintenance of oilfield infrastructure, pressure testing is a key process to ensure the safety and reliability of pipelines, pressure vessels, and other equipment. Due to its stable chemical properties, nitrogen is an ideal medium for pressure testing. During testing, nitrogen is injected into the equipment at a certain pressure. According to Boyle’s Law, at constant temperature, the pressure of a gas is inversely proportional to its volume. By monitoring pressure changes, potential leaks or structural defects in the equipment can be accurately detected. For example, if there are small cracks in the equipment, nitrogen will slowly leak out, causing a pressure drop, which allows for the timely identification of safety risks.
(B) Advantages of Nitrogen in Pressure Testing
Compared to other testing mediums, nitrogen offers unmatched advantages. First, nitrogen is chemically stable and does not react with the metals or other materials inside the equipment, preventing corrosion or damage that could occur during testing. Second, nitrogen is widely available and can be generated on-site with nitrogen generators, making it a relatively low-cost option. Additionally, nitrogen is non-flammable and non-explosive, greatly reducing safety risks when conducting pressure tests in the flammable and explosive environments of oilfields. Furthermore, nitrogen is easy to release after testing and does not cause environmental pollution.
(C) Operational Process of Nitrogen Pressure Testing
- Preparation Before Testing: Perform a thorough inspection of the equipment to ensure it is correctly installed and free from obvious external damage. Connect the nitrogen supply system, including the nitrogen compressor, nitrogen generator, and the necessary pipelines and valves. Set the injection pressure and testing duration based on the equipment’s design requirements.
- Nitrogen Injection: Slowly open the nitrogen valve to inject nitrogen into the equipment at the set pressure and flow rate. During this process, closely monitor pressure changes to ensure a steady increase in pressure and avoid pressure shocks that could damage the equipment.
- Pressure Stabilization Testing: Once the nitrogen pressure reaches the predetermined value, maintain the pressure for a certain period, usually several hours or even days, depending on the type of equipment and the standards. During this time, use specialized testing instruments to conduct a comprehensive inspection of the equipment, focusing on areas such as welds and connections where leaks are likely to occur.
- Pressure Release and Result Evaluation: After the test is completed, slowly release the nitrogen from the equipment. Based on the recorded pressure changes and test results, assess whether the equipment passes the test. If the pressure does not significantly drop and no leaks are detected, the equipment passes; otherwise, repairs and retesting are necessary.
VI. Nitrogen Compressor: The Key Equipment for Pressure Boosting
(A) The Indispensable Pressurization Function
The nitrogen compressor is the key equipment in the nitrogen application system of the oil field, and its main function is to pressurize the produced nitrogen to the pressure level required for oil field operations. Oil field operations usually require the nitrogen pressure to reach dozens or even hundreds of atmospheres to meet the needs of injecting nitrogen deep into the oil layer or other high-pressure operations.
In the nitrogen flooding operation, in order to make nitrogen effectively displace crude oil, the nitrogen pressure generally needs to be increased to 30 – 50MPa. This requires the nitrogen compressor to have a strong pressurization capacity to ensure that nitrogen can overcome various resistances in the reservoir and achieve efficient oil displacement.
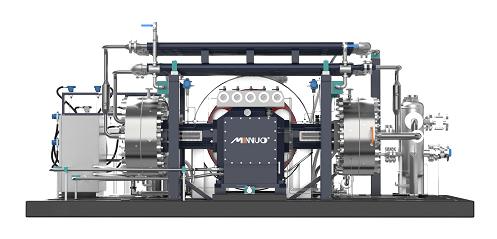
(B) Performance Requirements for Compressors
Explosion-proof
In an oil field full of inflammable and explosive gases, the explosion-proof performance of the equipment is crucial.
MINNUO’s nitrogen compressor strictly follows international and domestic explosion-proof standards such as ATEX, IECEx and GB 3836 in the design and manufacturing process. A special explosion-proof structure design is adopted and the electrical components are explosion-proof processed to ensure that even in extreme cases, explosion accidents will not be caused by the spark or high temperature generated by the equipment. At the same time, the sealing performance of the compressor is optimized to effectively prevent gas leakage and further improve the safety of the equipment in the dangerous environment.
Stability
A high-quality nitrogen compressor must have stable pressurization performance and maintain stable pressure output during long-term operation. In operations such as nitrogen flooding, stable pressure can ensure the consistency of the oil displacement effect. Excessive pressure fluctuation may lead to uneven displacement effect in the oil layer and affect the recovery rate of crude oil. From the perspective of control theory, advanced pressure control systems can be used to accurately adjust and stably control the output pressure of the compressor.
Our nitrogen compressor is equipped with an independently developed advanced pressure control system, which can monitor and accurately adjust the output pressure in real time. During the long-term operation process, the pressure fluctuation is extremely small, ensuring the efficient and stable progress of operations such as nitrogen flooding and effectively improving the recovery rate of crude oil.
Adaptability
The environment of the oil field is complex and changeable, and there are harsh conditions such as high temperature, high humidity and sand and dust. Therefore, the nitrogen compressor needs to have good environmental adaptability and can operate normally under various harsh environments to reduce equipment failures caused by environmental factors.
With years of experience in oil field projects, MINNUO’s products have deeply optimized the lubrication system and cooling system in the design and manufacturing process, adopted high-temperature and corrosion-resistant materials and equipped with efficient heat dissipation devices, so that the nitrogen compressor can still operate stably under harsh environments such as high temperature, high humidity and sand and dust, greatly reducing the equipment failure rate.
High efficiency
In order to meet the needs of large-scale production in the oil field, the nitrogen compressor should have high compression efficiency, be able to process more nitrogen in unit time, improve production efficiency and reduce energy consumption.
We continue to invest in research and development, optimize the structural design of the nitrogen compressor, adopt the new compression cavity profile design and advanced manufacturing technology, effectively reduce gas leakage and improve the compression efficiency. While meeting the needs of large-scale production in the oil field, the energy consumption and operation cost are reduced, bringing significant economic benefits to oil field customers.
VII. Nitrogen Generator: The Core Equipment for Nitrogen Production
(A) The Core Position of the Nitrogen Generator
The nitrogen generator is the source equipment for the oil field to obtain nitrogen, and its performance directly determines the output, purity and production cost of nitrogen. A high-quality nitrogen generator can provide a stable and high-quality nitrogen supply for the oil field and is the basis for ensuring the application of nitrogen in the oil field.
(B) Working Principles of Two Main Nitrogen Production Technologies
Pressure Swing Adsorption (PSA) Nitrogen Production
The PSA nitrogen generator realizes nitrogen separation by using the difference in adsorption capacity of adsorbents for different gases. Commonly used adsorbents such as carbon molecular sieves have a strong adsorption capacity for impurity gases such as oxygen and carbon dioxide and a weak adsorption capacity for nitrogen under a certain pressure, so that nitrogen is enriched. By periodically changing the pressure, the adsorption and desorption processes of the adsorbent are realized and high-purity nitrogen is continuously produced.
The key to PSA nitrogen production technology lies in the optimization of adsorbent performance and adsorption process. At present, advanced PSA nitrogen production equipment adopts automatic control technology, which can accurately control the adsorption time, pressure and other parameters and improve the nitrogen production efficiency and nitrogen purity. From the perspective of adsorption kinetics, studying the adsorption rate and adsorption capacity of adsorbents for different gases and optimizing the adsorption process parameters can further improve the performance of PSA nitrogen production technology.
MINNUO’s PSA nitrogen generator uses independently developed high-performance adsorbents and combines advanced automatic control technology to accurately control the adsorption time, pressure and other parameters and achieve efficient nitrogen production. The purity of the nitrogen produced by our products usually reaches more than 99.9%, and under special processes, it can reach 99.999%, meeting the strict requirements of the oil field for high-purity nitrogen and providing reliable nitrogen guarantee for the development of special reservoirs and high-end oil well testing and other operations.
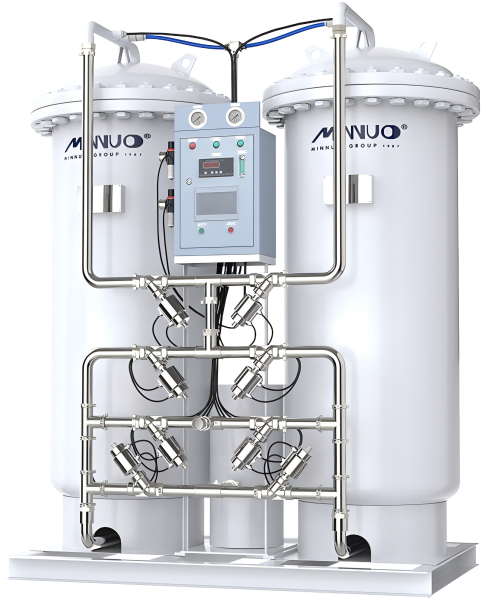
Membrane Separation Nitrogen Production
The membrane nitrogen generator uses special polymer membrane materials to separate gases based on the different permeation rates of different gases in the membrane. When air passes through the membrane module under pressure, small molecule gases such as oxygen and water vapor permeate through the membrane more easily than nitrogen, and the gas enriched with nitrogen is obtained on the other side of the membrane.
The membrane separation nitrogen production technology has the advantages of simple equipment structure, small volume and fast start-up speed, but its nitrogen purity is relatively low. In recent years, with the continuous development of membrane material technology and the research and application of new membrane materials, the performance of membrane nitrogen generators has been continuously improved. For example, by modifying the membrane material to improve its selectivity for nitrogen, the nitrogen purity of the membrane nitrogen generator can be effectively improved.
Our membrane nitrogen generator uses independently developed new membrane materials. By modifying and optimizing the membrane materials, while ensuring the simple equipment structure, small volume and fast start-up speed, the purity and output of nitrogen are effectively improved. The product can meet the requirements of the oil field for large nitrogen flow and relatively low purity operation scenarios, such as general gas lift production and large area inerting protection in the oil field, providing strong support for the efficient production of the oil field.
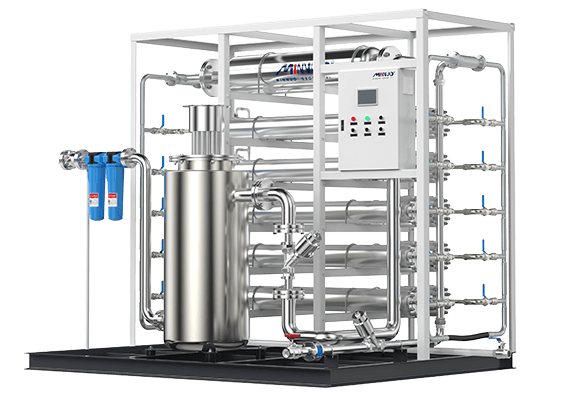
(C) Factors Affecting the Performance of Nitrogen Generators
Equipment Quality
The manufacturing process and equipment material of the nitrogen generator directly affect its performance and stability. High-quality equipment uses high-quality adsorbents and membrane materials and advanced manufacturing processes to ensure the long-term stability of the gas separation effect, reduce equipment failures and maintenance costs. For example, MINNUO uses high-precision processing technology to manufacture adsorption towers and membrane components to ensure the accuracy of their internal structure and improve the gas separation efficiency.
Operating Parameters
Operating parameters such as adsorption time, pressure and temperature have a significant impact on the performance of the nitrogen generator. Reasonably adjusting these parameters can optimize the nitrogen production process and improve the output and purity of nitrogen. In actual operation, the best operating parameters are determined by means of experiments and simulations and other methods, combined with the type and specific working conditions of the nitrogen generator. For example, MINNUO uses computational fluid dynamics (CFD) simulation technology to study the flow and separation process of gases in the nitrogen generator to optimize the operating parameters and improve the performance of the nitrogen generator.
(D) Detailed Comparison between PSA Nitrogen Production and Membrane Nitrogen Production
Purity Comparison
- PSA Nitrogen Production: PSA nitrogen production technology can produce high-purity nitrogen, and the purity usually reaches more than 99.9%, and under special processes, it can reach 99.999%. In oil field operations with extremely high requirements for nitrogen purity, such as the displacement operation of special reservoirs and some high-precision oil well testing scenarios, PSA nitrogen generators can meet the strict purity requirements. High-purity nitrogen ensures that no impurities are introduced in special operations and guarantees the operation effect and the long-term stability of the reservoir.
- Membrane Nitrogen Production: The purity of nitrogen produced by membrane nitrogen production is relatively low, generally between 95% and 99%. Although it can meet the needs in some general oil field operations with less strict purity requirements, such as conventional gas lift production and some well washing operations, it is not applicable in occasions with high purity requirements. The purity limitation of membrane nitrogen production mainly comes from the selective permeation performance of the membrane material. Although the membrane material is continuously improved at present, it is still difficult to reach the same high purity as PSA nitrogen production.
Flow Comparison
- PSA Nitrogen Production: The flow of PSA nitrogen generators is relatively small and is generally suitable for occasions where the demand for nitrogen is not particularly large but the purity requirements are high. Its equipment scale and gas production capacity are relatively limited. In the case of large-scale nitrogen demand scenarios, multiple devices may need to be operated in parallel. For example, in some small oil fields or special operation areas, the demand for nitrogen is small but the purity requirements are high, and PSA nitrogen generators can meet the needs.
- Membrane Nitrogen Production: The outstanding advantage of membrane nitrogen production technology is that it can achieve a large flow output. Its equipment structure is relatively simple and easy to scale up production, and it can quickly provide a large amount of nitrogen to meet the needs of large-scale operations in the oil field, such as large area gas lift production and large oil tank inerting. In the production of large oil fields, membrane nitrogen generators can quickly respond to the large-scale nitrogen demand and provide a guarantee for the efficient production of the oil field.
Equipment Cost and Maintenance Comparison
- PSA Nitrogen Production: The equipment cost of PSA nitrogen generators is relatively high because it needs to use special adsorbents and the equipment structure is relatively complex. However, due to the mature technology, its maintenance and repair are relatively convenient and the replacement cycle of adsorbents is relatively long, and the overall maintenance cost is within an acceptable range. In actual application, although the equipment investment of PSA nitrogen generators is large, the long-term operation cost is relatively stable, which is suitable for oil field operations with high requirements for nitrogen purity and relatively stable production scale.
- Membrane Nitrogen Production: The equipment cost of membrane nitrogen generators is relatively low, the equipment structure is simple, the volume is small and the floor area is small. However, the service life of its membrane components is limited and needs to be replaced regularly. The cost of membrane components increases the maintenance cost to a certain extent. Moreover, the membrane nitrogen generator has high requirements for the pretreatment of the inlet gas. If the pretreatment is improper, it is easy to cause the blockage of the membrane components and affect the equipment performance.
Application Scenario Adaptability Comparison
- PSA Nitrogen Production: It is suitable for oil field operations with extremely high requirements for nitrogen purity and relatively small nitrogen demand, such as the development of special reservoirs and high-end oil well testing. In these areas, high-purity nitrogen is crucial for ensuring the operation effect and the long-term stability of the reservoir. Although the nitrogen quantity needed is not large, the strict purity requirements make PSA nitrogen production the top choice.
- Membrane Nitrogen Production: It is more suitable for operation scenarios where there is a large demand for nitrogen flow but relatively low requirements for purity, like general gas lift oil production and large-scale inerting protection in oil fields. In such scenarios, a substantial amount of nitrogen is required, while the purity standards are more lenient. Membrane nitrogen generators can supply large volumes of nitrogen at a lower cost, thus meeting production demands.
To present a more intuitive comparison, the following table is provided:
Comparison Items | PSA Nitrogen Production | Membrane Nitrogen Production |
Nitrogen Production Principle | Based on the difference in the adsorption ability of adsorbents for oxygen and nitrogen, achieving nitrogen-oxygen separation through periodic pressure changes | Utilizing the different permeation rates of each component in air through polymer membranes for separation |
Nitrogen Purity | 99.9% – 99.9995% | 95% – 99.5% |
Flexibility of Yield Adjustment | Wide range of production adjustment. It can be flexibly adjusted by increasing or decreasing the number of adsorption towers or adjusting the adsorption cycle, etc. | The adjustment range is relatively narrow, mainly depending on the specifications of membrane components and the capacity of the compressor |
Stability | The equipment is mature, easy to operate, highly automated, and has high operational stability | Slightly less stable compared to PSA nitrogen production |
Floor Space | The equipment structure is relatively complex, occupying a larger area | Simple structure, small volume, and small floor space |
Installation Convenience | The installation process is relatively complicated, requiring a certain amount of space to install the equipment and supporting facilities | Simple to install, without the need for complex pipeline connections and large-scale foundation construction |
Energy Consumption | During operation, valves switch frequently and pressure changes occur, resulting in relatively high energy consumption | The main energy consumption is concentrated in the compressor, with relatively low energy consumption |
Initial Investment | High one-time purchase cost and installation cost | Relatively low initial investment cost |
Applicable Scenarios | Oil field projects that require high nitrogen purity, large-scale centralized gas supply, and high requirements for equipment stability and production adjustment flexibility | Oil field projects with strict space limitations, limited budgets, nitrogen purity requirements below 99.5%, and low requirements for production adjustment flexibility |
VIII. Conclusion
In general, when choosing nitrogen application schemes and related equipment, oil field customers need to comprehensively consider various factors such as operation requirements, costs, and equipment performance to achieve the best production efficiency and safety guarantee.
MINNUO will also continue to invest in research and development, keep innovating, and provide higher-quality products and services for oil field customers. If you want to obtain nitrogen-related solutions, please feel free to contact us!